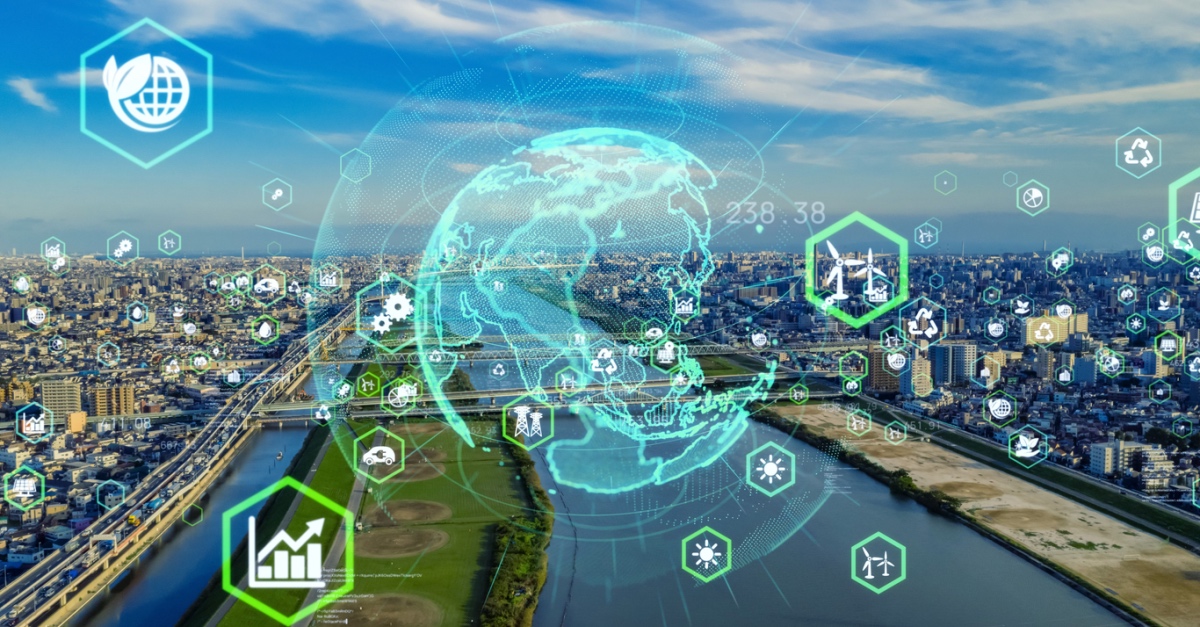
The world of logistics and transportation cannot afford to slow down, and the trend toward sustainable logistics is working hard to catch up. Demand for shipping and delivery services is only increasing in a fast-moving, interconnected global economy. But with this growth comes greater pollution levels from vehicles and logistics networks.
For this reason, it shouldn’t be surprising that 75% of logistics companies have a focus on sustainability, according to a May 2024 survey by the Germany-based Logistics Hall of Fame. A majority of respondents rated the risk of financial loss due to climate change as “medium to high.”
This is why major efforts are underway to reduce trucking-generated pollution by implementing a sustainable logistics program. These include efforts to optimize routing, grow alternative fuel fleets, increase the use of automation, enforce stricter emissions standards, and ramp up intermodal transportation.
Optimized routing, in particular, has emerged as a powerful tool to not only reduce transportation costs but also significantly minimize carbon emissions, making logistics operations more sustainable.
The Environmental Impact of Logistics
Transportation contributes more than a third of all CO2 emissions globally, with nearly two-thirds of that coming from trucking, according to the International Energy Agency (IEA). In addition, transportation relies on petroleum products for nearly 91% of its energy, down just 3.5 percentage points from the early 1970s.
Excessive fuel usage in everything from long-haul trucking to last-mile delivery, traffic congestion, and poorly planned routes contribute to higher CO2 emissions. At the same time, regulatory pressure and consumer demand for more sustainable business practices are forcing companies to adapt.
The Basics of Route Optimization
Route optimization tools use advanced algorithms and predictive analytics, parsing historical and real-time data to identify the most efficient delivery routes. Factors taken into account include traffic conditions, weather, vehicle capacity, delivery windows, and road restrictions.
Many routing tools within a transportation management system (TMS) also include load optimization capabilities, enabling companies to maximize their available freight capacity and improve key metrics like revenue per mile, cost per delivery, and fleet utilization.
State-of-the-art route optimization tools employ dynamic multi-day route planning and scheduling across trucking modes, everything from LTL, TL, middle mile, last mile, private fleet and dedicated transportation services.
Reducing Fuel Consumption and Carbon Emissions
As route optimization enables companies to reduce the number of miles driven, an immediate, tangible benefit is a significant saving on fuel consumption.
These tools also allow drivers to avoid areas of traffic congestion, helping to improve on-time delivery performance. This not only reduces truck dwell time and, thus, tailpipe emissions, but also increases customer satisfaction.
By optimizing load capacity, companies can put fewer trucks on the road, further reducing fuel usage and emissions — further driving sustainable logistics.
The Role of Real-Time Data in Sustainable Routing
Access to real-time data on traffic, weather, and road conditions allows for dynamic rerouting to avoid delays and minimize emissions. Traffic data can come from GPS systems and platforms like Google Maps or Waze for information on congestion, accidents, and road closures.
Weather data from apps like The Weather Channel or OpenWeatherMap provide updates on conditions (thunderstorms, high wind, fog, snow) that might affect a trip, rerouting if necessary. Telematics and sensors take in data on vehicle location, speed, fuel usage, and status from onboard systems or fleet management software.
Updates from order management systems (OMS) on delivery windows and customer availability also become part of the routing equation, as does data on weight or height restrictions and road closures from transportation departments. Routing software also tracks fuel efficiency and vehicle performance, reducing environmental impact.
Other Benefits of Route Optimization
In addition to reduced fuel consumption and lower operating costs, route optimization enables faster, more reliable deliveries, improving customer relationships and fostering loyalty.
Optimized routing also helps companies meet their environmental goals through sustainable logistics. This includes compliance with government regulations and qualification for certifications such as LEED, ISO14001, and SmartWay.
Route Smarter, Stay Greener
Route optimization improves logistics efficiency and plays a crucial role in reducing carbon emissions. An investment in this technology helps drive both sustainability and competitiveness in a business climate that increasingly values environmental responsibility. By embracing sustainable logistics practices through the use of these tools, companies can reach their goals while driving down costs through efficiency gains.
Tramm, an innovator in supply chain technology, has developed an end-to-end TMS platform that combines route planning, load building, transporter management, a supply chain control tower, and a powerful mobile app. With this end-to-end approach, Tramm has solved the problem of fragmented supply chain systems by integrating key functions into a unified, scalable platform.
Tramm’s Planning and Optimization Module handles complex routing environments, accounting for variables such as rules and constraints that accurately reflect on-the-ground transport operations. It allows users to easily adapt their plans based on changing needs, including “what if” visualization and scenarios that enable real-time adjustments. A load builder/stackability app lets them automatically plan loads that are tightly synced with capacity and route optimization.
To find out how Tramm’s unified approach can drive transportation efficiency and cost savings while helping you realize sustainability goals, request a demo today.
Related Resources
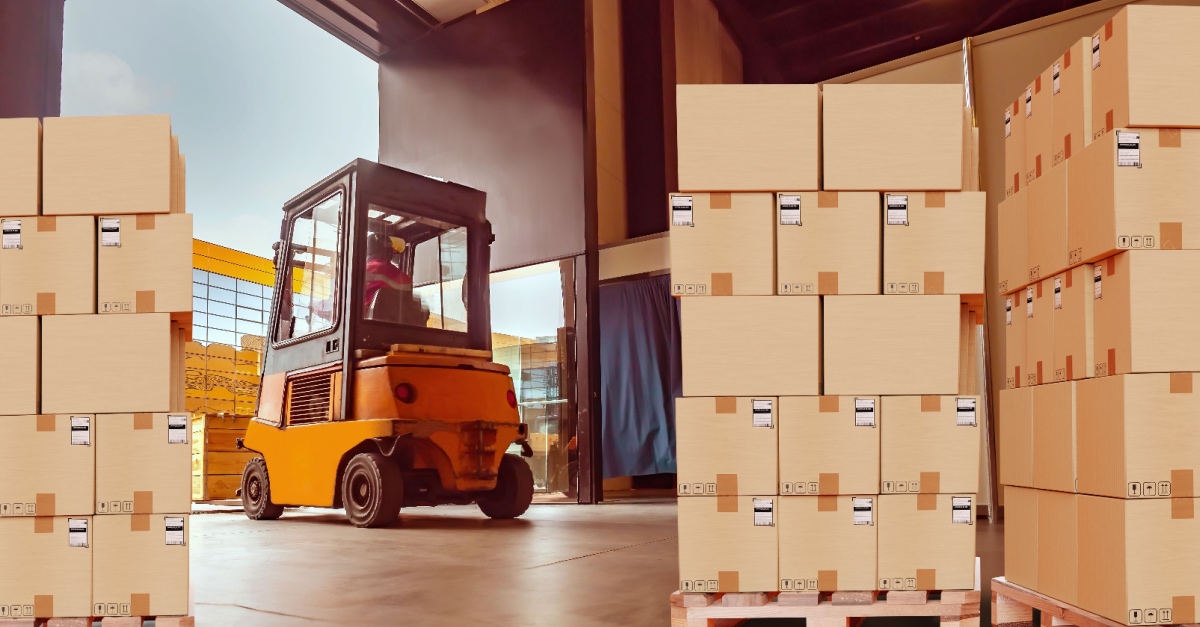
Managing Large Order Loads to Reduce Split Shipments
In the world of B2B commerce, having an efficient order management process is a baseline capability. Especially when large order loads are involved, the ability to achieve a high percentage of orders shipped complete drives significant transportation savings, as split shipments eat away at margins.
There are several factors that drive an increased reliance on split shipments for large order loads, sometimes acting in combination to exacerbate the issue. These include how inventory is distributed in a network, the pressure on stock levels from large orders, and the operational strain it can cause. That’s why order management precision and efficiency is at such a high premium, especially when disruptions like a major port strike throw a wrench in the works.
This article examines split shipments and the issues they cause within the supply chain and distribution and explores some best practices to avoid them. The aim is to help reduce operating expenses, improve product availability, and increase customer satisfaction.
Definition and Causes of Split Shipments
A split shipment happens when an order is divided into multiple shipments due to low stock levels, logistical constraints, or both. Often, businesses feel forced to ship what’s available immediately and send the rest later, hoping that customers can get by on the partial order in the meantime.
Some common causes of split shipments on large B2B orders include the following:
- Multiple suppliers: Variations in supplier lead times or stock availability can cause parts of the order to arrive at different times.
- Order complexity: Large orders often involve diverse products with different handling, storage, or shipping requirements. For instance, temperature-sensitive or hazardous goods requiring specialized transportation often lead to separate shipments.
- Order prioritization: High-priority, in-demand products are time-sensitive, which can lead to shipping what’s on hand separately while waiting for replenishment to send the rest.
- Warehouse fulfillment: Large orders can tax the resources of warehouse operations. SKUs stored in different locations or those requiring a different picking process can cause delays, leading to split shipments.
- Backorders and lead time variation: Some items have significantly different supplier lead times, forcing businesses to ship only a portion of their available inventory and put the balance on backorder.
- Inefficient systems: Without an advanced order management system (OMS), businesses lack real-time inventory visibility across multiple locations. This leads to fragmented fulfillment decisions and more split shipments.
The High Cost of Split Shipments
While some split shipments are inevitable or unavoidable due to external factors, costs go up along with higher frequency. Transportation is clearly the highest direct cost, as it’s generally the second highest expense as a percentage after labor, and more trips are required. There’s also the added complexity of scheduling additional pickups with transporters.
Speaking of labor, split shipments also hit this cost center, as they lead to more man-hours spent preparing orders through picking and packing.
Indirect costs include damage to customer relationships and reputation and the potential loss of future business. B2B customers rely on complete orders to meet production schedules or product demand. As a result, many retailers have implemented on-time in-full (OTIF) requirements. The idea is to enforce greater supply chain optimization by tight collaboration among retailers, brands, transporters, and logistics service providers.
Failure to meet OTIF requirements results in fines and penalties. A McKinsey study found that many retailers in North America are tightening OTIF requirements by narrowing delivery windows and increasing fines while revising the definition of in-full delivery.
A higher incidence of split shipments can reflect deeper issues of poor inventory management, such as stock imbalances or inefficient replenishment processes. Finally, they contribute to higher carbon emissions from the additional truck trips required.
Other Split Shipment Headaches in B2B
Split shipments introduce complexities that impact multiple areas of operations, including order tracking, invoicing, and customer communication. Each contributes to inefficiencies, often leading to higher costs, increased labor, and a decline in service quality.
Tracking Complexity
When shipments are split, tracking the order status becomes more complicated because different segments move independently through the supply chain. Logistics teams have to track each portion of the order separately, from inbound inventory to fulfillment and delivery. This involves monitoring multiple tracking numbers, the status of transporters, and estimated delivery times.
Managing Multiple Invoices
Split shipments often lead to multiple invoices, complicating accounts payable for both the shipper and customer, including reconciliation of multiple invoices against the original order. Each invoice might include different shipping costs, taxes, and fees, adding to administrative overhead. In some cases, customers might withhold payment until the entire order is delivered, adding more complexity and delaying closing the transaction.
Customer Communications
In B2B transactions, logistics and delivery impact a customer’s production schedules, inventory levels, and downstream operations. Shippers need to manage expectations around timing, coordination, and delivery schedules. Customers often rely on complete shipments to avoid production downtime, which causes frustration and the pain of adjusting internal processes.
Split shipments also require customers to coordinate with receiving teams across multiple deliveries. Additional labor and resources are needed to accept, inspect, and verify each portion of the order upon arrival.
Leveraging Technology to Optimize B2B Order Management
Advances in technology for supply chain and logistics have made it easier for businesses to optimize their inventory and order management processes in order to reduce the incidence of split shipments. Here are some examples.
WMS
A warehouse management system (WMS) provides real-time updates on inventory levels, enabling better decision-making and reducing stock-outs that lead to split shipments. Most systems can also automate inventory replenishment to ensure that items in high demand remain in stock, reducing the need for split shipments.
OMS
An order management system (OMS) integrates order data from various sources (e-commerce platform, ERP, CRM, WMS, etc.), providing visibility into inventory availability. This helps drive a higher percentage of “order complete” confirmations before shipment. An OMS also has consolidation logic for prioritizing full order fulfillment vs. partial shipments.
Tramm, a developer of a leading unified supply chain management platform, combines a powerful OMS within its transportation management system (TMS) suite. This integrated approach provides end-to-end visibility and control over order fulfillment and shipping processes. Tramm’s Order Management Module ensures that orders are fully consolidated before being released for shipment, while the TMS manages transportation in the most efficient, cost-effective manner.
Using real-time data synchronization, Tramm’s integrated approach ensures that any changes in order status, inventory levels, or shipping schedules are immediately reflected across both systems. This allows the OMS to quickly adjust fulfillment strategies if stock availability or transporter issues arise, reducing the need to rely on split shipments.
Predictive Analytics and Demand Forecasting
Predictive analytics tools tap the power of AI to enable proactive inventory management. By more accurately forecasting demand and optimizing inventory levels, both stockouts and split shipments are reduced. This technology enables users to foresee potential supply chain disruptions and adjust fulfillment strategies accordingly.
Automated Fulfillment and Transporter Routing
Fulfillment automation reduces errors in picking/packing, allowing a higher percentage of full orders to be processed and minimizing the need for split shipments.
Smart routing automatically directs orders to the most appropriate warehouse or fulfillment center, optimizing shipments and reducing transportation costs. Tramm’s Planning & Optimization Module uses advanced algorithms and visualization tools to drive better, faster load and routing decisions. The result is operational cost savings, including reduced split shipments and highly responsive planning capabilities.
Supplier Collaboration and Data Sharing
Collaborative planning includes sharing inventory and demand data with suppliers, improving stock replenishment, and reducing the likelihood of split shipments. By employing Vendor-Managed Inventory (VMI), suppliers manage stock levels, helping ensure that products are consistently available. This minimizes the need for split shipments due to out-of-stocks.
Best Practices to Minimize Split Shipments in B2B Order Management
Companies can take several steps to improve their order management processes, increase efficiency, and increase the percentage of “shipped complete” orders.
Centralized Inventory Management
Centralized inventory involves keeping all stock in one primary location, such as a warehouse, fulfillment center, or other storage facility. This central hub typically manages not only inventory but also key logistics functions like order processing and fulfillment.
In a centralized inventory system, the majority of operations, including order management and distribution, are handled from this single location, even when there are multiple sales channels or retail outlets. This strategy reduces the need for split shipments due to inventory imbalances.
Order Consolidation Policies
Order consolidation involves combining multiple orders into a single shipment. This can be done by centralizing items from multiple orders into a single location or by combining multiple orders from different sales channels into a single system.
Order consolidation can benefit businesses in several ways. This includes lower transportation costs based on economies of scale, better management of stock levels due to fewer shipments, overall simplified logistics, and a better customer experience through more complete orders.
Smart Reordering Strategies
Smart reordering is a rules-based, automated process utilizing data analytics and AI to manage inventory levels and optimize replenishment. Unlike traditional reordering, which relies on manual tracking or fixed schedules, smart reordering uses real-time data (sales trends, demand forecasting, lead times, supplier performance, etc.) to predict when SKUs will need to be replenished.
This approach helps ensure that critical and/or high-demand products are always in stock, preventing backorders and reducing the need for split shipments.
Transparent Customer Communication
This seems like an obvious point, but too many organizations fail to keep customers updated on order status. This is especially important when unexpected drops in inventory levels or logistics snafus require a split shipment.
Always give customers the option of waiting for replenishment to send a complete order or receiving a partial shipment first. In some cases, the added expense of expedited transportation comes into play to make things right and keep to their schedule.
Continuous Monitoring and Adjustment
Regularly analyzing order data helps identify patterns that lead to increases in split shipments. By tracking trends in demand, stock levels, and fulfillment performance, you can proactively adjust inventory management, including redistributing stock across locations or improving order consolidation processes.
Leaning On Technology to Optimize Large Order Loads
Minimizing split shipments is important to maintain supply chain efficiency and reduce transportation costs. Software such as OMS, WMS, and predictive analytics tools can improve inventory management and streamline fulfillment processes. Best practices such as smart reordering, order consolidation, and continuous monitoring help reduce the incidence of split shipments.
Tramm integrates transporter management, route optimization, order management, customizable dashboards, and a control tower to optimize routing and order allocation. When shipments do need to be split, Tramm automates the process based on operational and resource requirements.
Tramm’s FleetVision Module gives users access to precise real-time data and insights. With a better understanding of fleet operations on a granular level, they can manage each load more effectively and implement performance improvement measures. The result is greater efficiency, reduced costs, and improved customer satisfaction.
To learn more about how Tramm can drive measurable improvement in your supply chain and logistics operations, request a demo today.
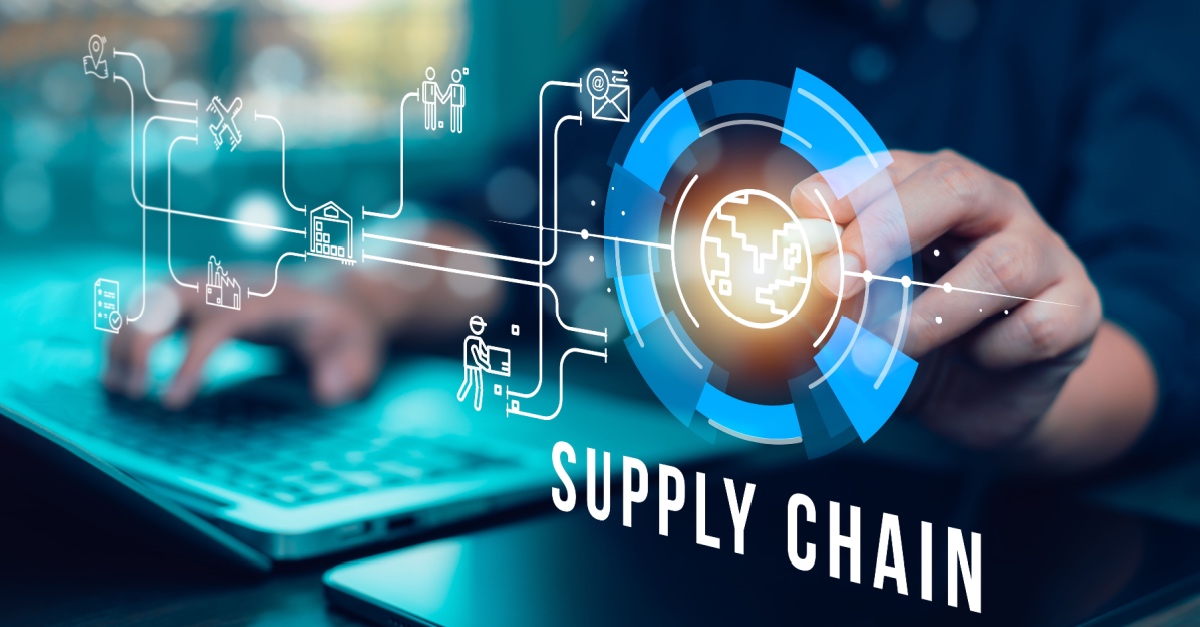
Synchronized Logistics: Leveraging An Integrated TMS for Real-Time Supply Chain Management
An integrated supply chain TMS helps make tight partner collaboration and data collection from multiple sources possible so goods flow smoothly, SLAs are hit, and production stays on track.
It’s also a key element in synchronized logistics, a process that businesses lean on to manage multiple complex systems. This involves pulling together and analyzing data from disparate sources, all of which touch the supply chain in some way: transportation management systems (TMS), warehouse management systems (WMS), enterprise resource planning (ERP), and even yard management systems (YMS). Using data analytics, synchronized logistics pulls together insights that can then be applied to various supply chain processes.
In this context, an integrated supply chain TMS can achieve synchronized logistics by enhancing business intelligence and optimizing all aspects of transportation. This, of course, has multiple benefits up and down the supply chain, such as faster inventory turns, better delivery metrics, and improved asset utilization, among others.
An integrated TMS uses advanced business intelligence to optimize logistics and transportation by analyzing large sets of real-time and historical data. It helps identify patterns and inefficiencies, predict delays, and recommend optimal routes. Using predictive analytics to forecast demand can optimize capacity utilization and automate decision-making, such as selecting the most cost-effective carriers or adjusting delivery schedules.
An integrated TMS enables more precise planning, cost control, and supply chain efficiency by incorporating data from ERP, WMSs, and other systems. This helps companies improve planning and execution, reduce delays, and respond quickly to disruptions. Using AI-powered data analytics, businesses can fine-tune their operations and keep costs in check.
As the need for real-time supply chain visibility grows, the role of an integrated supply chain TMS becomes even more critical. Its ability to synchronize logistics and provide actionable insights helps companies stay competitive in an increasingly dynamic market.
What is an Integrated TMS in the Supply Chain?
An integrated TMS is a comprehensive platform designed to streamline the core functions of supply chain management: planning, execution, and optimization of transportation activities. It helps businesses plan efficient routes, execute shipments, and optimize delivery schedules to reduce costs and improve performance.
It also helps meet heightened performance expectations by providing visibility and agility across the supply chain. Unlike a traditional TMS with limited connectivity, an integrated TMS hooks into multiple complementary software systems. Creating a cohesive information flow across the supply chain enables more informed decision-making and better cross-functional collaboration. Businesses benefit from real-time tracking, updates, and greater visibility into logistics operations.
The Importance of Real-Time Supply Chain Management
Customers in both B2B and B2C are demanding faster delivery times, more accurate ETAs, tight delivery windows, and real-time updates on order status. Call it the “Amazon effect,” driven by the higher service level expectations created by the mega e-commerce company turned logistics powerhouse. Especially in a tighter economy, there is little margin for error in terms of costs, the balance sheet, and customer churn.
Real-time supply chain management involves continuously monitoring and managing supply chain activities as they happen. This is where synchronized logistics comes into the picture. Real-time data from integrated systems provides immediate visibility into inventory, shipment status, and fulfillment operations. This allows businesses to make quick, informed decisions, optimize routes, and adjust to changing conditions. The result is increased efficiency, cost savings, and improved customer service.
Key benefits of real-time supply chain management include:
Quick response to disruptions: Real-time supply chain management enables businesses to respond swiftly to issues like traffic, port congestion, or weather delays. With immediate access to updated data, they can quickly adjust routes, reschedule shipments, and notify customers, minimizing delays and maintaining operational efficiency.
Optimized route planning: Real-time data from TMSs allows businesses to dynamically optimize routes based on current conditions such as traffic or road closures. This reduces transit times, improves fuel efficiency, and enhances on-time delivery rates, leading to cost savings and improved KPIs.
Improved customer satisfaction: Accurate real-time tracking ensures customers receive up-to-date information on shipment status, including greater accuracy in delivery estimates. This transparency and proactive communication build trust and loyalty by enhancing customer experience (CX), helping companies exceed delivery expectations, and improving customer satisfaction.
Core Features of an Integrated TMS That Supports Synchronized Logistics
An integrated supply chain TMS offers a wide array of features designed to improve supply chain management and logistics flow:
Real-Time Tracking and Visibility
A supply chain TMS allows you to monitor each shipment from order to delivery by providing continuous updates on shipment location, inventory status, and delivery progress. This level of transparency allows you to quickly address potential issues (delays, misrouting, breakdowns) before they escalate. The system’s ability to provide real-time views into supply chain flow improves accountability and efficiency.
Advanced Data Analytics
Integrated TMS platforms use predictive analytics to anticipate delays, optimize routes, and improve decision-making. Predictive and even prescriptive insights allow businesses to proactively avoid disruptions and refine logistics strategy.
Automation and Collaboration
Automation tools facilitate freight scheduling, real-time communication with carriers, and stakeholder collaboration. This reduces manual intervention and enables teams to focus on higher-value tasks.
Seamless Integration
An integrated TMS connects with other systems to synchronize supply chain operations. This ensures data flows smoothly between departments, teams, and partners, helping streamline processes and reduce delays.
Overcoming Common Supply Chain Challenges with Integrated TMS
An integrated TMS helps businesses address several common supply chain challenges:
Reducing delays and inefficiencies: Real-time updates allow companies to anticipate and avoid delays. With real-time visibility, businesses can reroute shipments or adjust schedules to minimize disruptions.
Improving demand forecasting and inventory management: Data generated by a TMS helps logistics planners maintain lean inventories while still meeting customer demand. With accurate, up-to-date information on shipment status and inventory levels, they can more closely align supply with demand, reducing the risk of stockouts or overstocking.
Adapting to market changes: Market volatility and changes in consumer behavior can disrupt supply chains. An integrated TMS helps businesses become agile through real-time adjustments to routes, carriers, or schedules in response to changing conditions.
The Role of Data in Synchronized Logistics
Data is the backbone of synchronized logistics. An integrated TMS collects, processes, and analyzes vast amounts of data to drive more informed decision-making.
A TMS provides real-time data, enabling better decision-making in procurement, route optimization, and warehouse management. Accurate, timely information helps businesses be more proactive and improve overall efficiency.
Many advanced TMS platforms incorporate AI and machine learning algorithms to predict risks, optimize freight rates, and automate repetitive tasks. These technologies enhance the system’s ability to make real-time adjustments, delivering improved operational efficiency and reduced costs.
By leveraging real-time data, businesses can provide more accurate information to customers about shipment status, improving transparency and loyalty. Data-driven synchronized logistics enhances CX by ensuring timely deliveries and proactive communication.
Choosing the Right Integrated TMS for Your Business
Some attributes of an integrated TMS include its intuitive UI, which makes it easy for nontechnical users to manage both owned and contracted transportation assets. This includes streamlining aspects of transportation management, such as contracts and payments.
Scalability is another important feature, as well as a cloud architecture and ease of integration with other systems through API connections. A supply chain TMS should also be customizable and rules-based, adaptable to prioritize the execution of last-mile delivery, international shipping, or retail replenishment. Mobile workflows, master data attributes, exception management, self-reporting, and business intelligence should all be easily configurable based on your business needs.
The importance of provider reliability cannot be overstated. Look for a company that offers robust customer support, ongoing training, and regular system updates to address evolving industry and business needs. This is a recipe for long-term success, giving you the ability to maximize system capabilities.
An Integrated TMS: Creating the Future of Supply Chain Efficiency
An integrated supply chain TMS plays a pivotal role in powering synchronized logistics so businesses can streamline operations and respond in real time to supply chain challenges. Consolidating data from multiple systems enhances visibility, optimizes routes, and minimizes disruptions. Companies can make informed decisions, improve delivery performance, and reduce costs through advanced analytics and automation. These next-generation systems ensure a more agile, efficient, and customer-centric supply chain.
Tramm TMS is the first SaaS platform using advanced technology to enable companies to easily manage all transportation assets, both owned and third-party, from the first mile to the last mile.
It is purpose-built to streamline supply chain operations, synching data to create a single source of truth. By eliminating data silos and tapping the power of AI-driven insights, Tramm streamlines processes and ensures a consistency of action across the supply chain.
With its modular, scalable architecture, Tramm’s solution set includes an order management system (OMS), a visibility and control tower module, a global transporter module, a dashboards module, and a driver app. Its platform marries flexibility with optimization, powering a customer-centric approach that delivers measurable results. To learn more about Tramm’s ability to power synchronized logistics and increase supply chain efficiency in your organization, request a demo today.
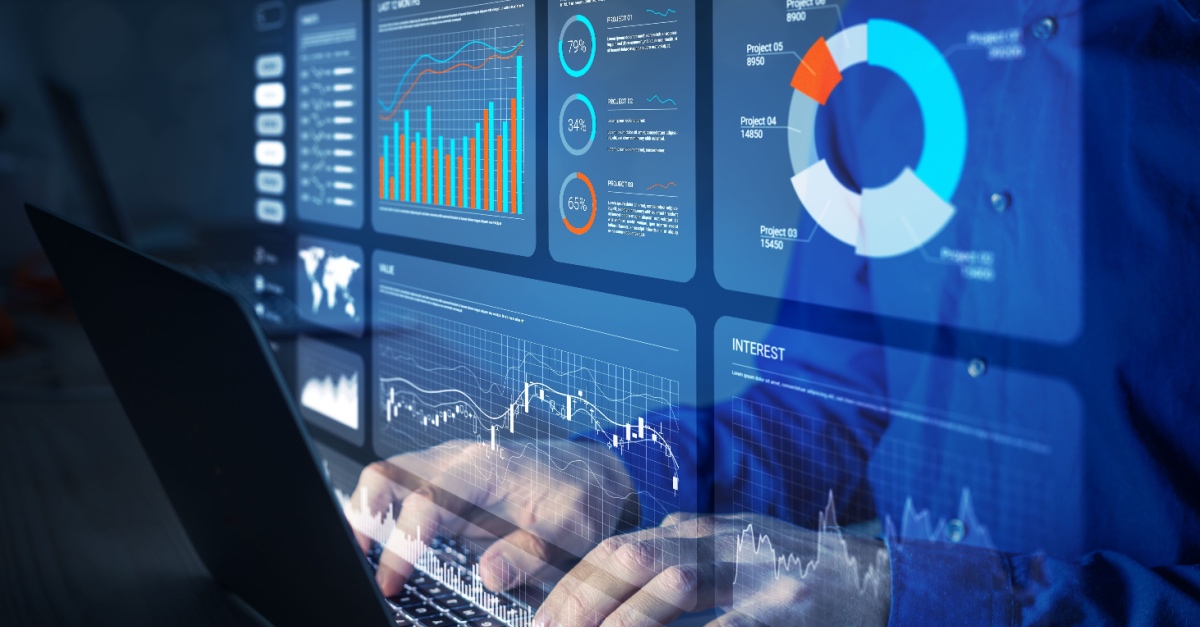
Supply Chain Analytics for Supply Chain Management: Three Tactics To Improve Efficiency
Supply chain analytics is the process of studying historical, transactional, and real-time data in order to uncover ways to improve supply chain efficiency and performance. As such, it is a vital function of any organization involved in the transportation of goods, addressing not only cost management but performance management.
And supply chain management has grown more complex, with frequent disruptive factors the norm, on top of major pandemic shocks that exposed flaws needing strategic resets. In this context, supply chain analytics are called upon more than ever to surface patterns and insights that drive intelligent decisions.
This article will present three key tactics for effectively implementing supply chain analytics, helping companies drive down costs and improve performance.
Modern Supply Chain Management Demands Modern Supply Chain Analytics
To define it further, supply chain analytics pulls in data from throughout the supply chain (procurement, manufacturing, inventory, orders, and distribution) for deep analysis in order to predict and improve performance. This data comes from external (carriers, partners, suppliers) as well as internal (ERP, SCM, TMS, WMS, inventory management, OMS, etc.) sources.
The ability to gain supply chain efficiency by improving data analytics can achieve a number of important business goals. This includes (but is not limited to):
- Minimizing inventory carrying costs
- Optimizing order fulfillment
- Proactively managing material costs
- Avoiding stockouts and overstocks
- Managing suppliers and purchases
Supply chain analytics also empowers businesses to engage in data-driven decision-making in the supply chain that can lower costs and improve resiliency and responsiveness. They can anticipate challenges and adapt to market fluctuations, helping them maintain a competitive edge even as challenges proliferate.
Three Tactics for Effective Implementation of Supply Chain Analytics
In order to receive the full benefit of supply chain analytics, companies need to look at it strategically and implement tactics designed to drive results in supply chain management. Here are three ways to achieve this.
Tactic 1: Integrate Data Across the Entire Supply Chain
The ability to gain a unified view of data across the supply chain is foundational in making supply chain analytics work effectively and glean actionable insights. This requires data feeds, ideally through API integrations, from all internal and external sources.
It’s often easier said than done. Data silos and fragmented systems, unfortunately, are still a thing. Enterprise systems that can’t communicate without IT intervention pose a challenge to integration.
One surefire way to achieve effective data integration is by using a true supply chain TMS that centralizes data from across multiple sources, such as those listed above (orders, shipments, inventory, etc.). A key prerequisite is compatibility with your current tech stack (ERP, WMS, TMS, etc.).
Tramm is a comprehensive TMS that is purpose-built to streamline supply chain operations within a unified platform approach. Its integration capabilities unify data from across the supply chain, creating a single source of truth. Tramm’s consolidated platform helps teams pull together actionable insights based on real-time data. This unified approach eliminates data silos, streamlines processes, and ensures consistency of actions across the supply chain.
Tactic 2: Implement Real-Time Analytics for Proactive Decision-Making
Real-time analytics is the process of analyzing and responding to data as it's generated, with the goal of providing quick insights to help users make better-informed decisions. Conversely, relying on delayed or outdated data acts as a drag on supply chain performance.
It's often used in applications where the timeliness of data is critical, such as in supply chain and logistics. Artificial intelligence and its cousin, machine learning, have added the ability to quickly read, comprehend, and correlate data from across sources, advancing real-time analytical capabilities.
Adopting a TMS with real-time data processing and monitoring capabilities ensures a seamless data flow and communication between systems and stakeholders. For example, Tramm’s FleetVision control tower module provides real-time vehicle tracking through integration with telematics, and status updates. It enables communication with all stakeholders via WhatsApp, SMS, or email for visibility into delivery status, deviations, and reporting.
Tactic 3: Utilize Advanced Analytics for Predictive and Prescriptive Insights
In the context of supply chain management, predictive analytics takes historical, transactional, and real-time data to create models that identify patterns for risks and opportunities. This helps guide decision-making by anticipating specific future events.
Prescriptive analytics takes this process a step further. It pulls together insights gleaned from predictive data analysis to suggest optimal actions, anticipating and solving potential issues before they arise.
This type of advanced capability for supply chain management involves integrating AI and machine learning to drive both predictive and prescriptive analytics. Staff must be adequately trained and processes aligned to take full advantage of these tools for real-time decision-making that drives greater supply chain efficiency.
Tramm’s advanced analytics include both predictive and prescriptive tools that optimize routing, and risk management. Tramm enables businesses to anticipate future challenges and take proactive steps in response. This type of real-time decision-making improves supply chain efficiency and resiliency.
Analytics Power Better Supply Chain Management
In reality, supply chain analytics is what drives supply chain management. The ability to pull in and quickly analyze internal and external data to formulate strategies and inform decisions is a foundational discipline. Mix in a complex global economy and disruptive events, and this capability becomes even more critical.
Tramm gets this, which is why it has developed a comprehensive suite that helps companies address multiple aspects of supply chain management. Its innovative supply chain TMS provides in-depth performance analytics backed by real-time data. Users gain planning and route optimization (Planning and Optimization Module), transporter management (Transact Module), real-time visibility (FleetVision Module) and impactful business insights (Dashboard Module), and much more. To learn more about how Tramm can transform your supply chain management, request a demo today.
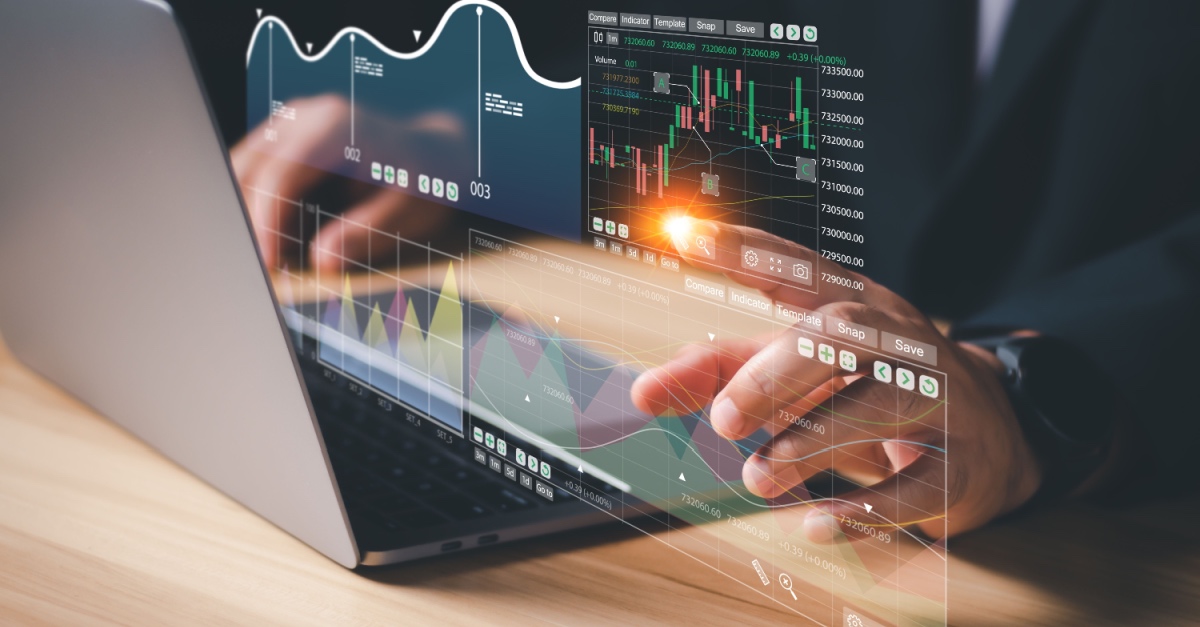
Smarter Shipping: Leveraging a Supply Chain TMS for Enhanced Business Intelligence
As we’re not yet living in the age of “Star Trek,” where people and things can be transported by breaking down and then reassembling molecules thousands of miles away (Elon Musk: take note), we here on Earth still count on shipping and logistics. By land, sea, and air, massive amounts of cargo are moved every day to keep global commerce humming. And a modern supply chain TMS (transportation management system) is a key technology that helps make it happen more efficiently.
Intelligent shipping combines business intelligence, planning, and execution tools, along with strategy and process, to optimize routing, scheduling, loading, communication, transporter management, etc. There are many primary and secondary benefits, including faster, more accurate deliveries, cost savings, improved customer satisfaction, better driver engagement and retention, and improved inventory management and demand forecasting.
A true supply chain TMS can help you achieve your goal of intelligent shipping by enhancing business intelligence and optimizing all aspects of logistics and transportation.
The Role of Supply Chain Analytics in Global Transport Operations
Supply chain analytics help organizations both keep track of and improve operational performance across various interdependent functions. All of that activity is throwing off tons of data, requiring sophisticated systems to synthesize and analyze, produce insights, and make recommendations. Increasingly, this is done by automating what had been manual processes, such as demand forecasting and route optimization.
The capabilities of supply chain data analytics have advanced significantly in recent years, increasing operational efficiency across all phases of transportation and logistics. For example, modern systems can assess risks associated with everything from geopolitical disruptions and natural disasters to freight capacity and supplier performance. Companies can then develop contingency plans and make better-informed decisions to mitigate these risks.
An advanced supply chain TMS can track KPIs such as the percentage of on-time deliveries, delivery error rate, cost per mile and cost per unit, load utilization percentage, average delivery time, and order cycle time. All of these metrics act as a barometer of business performance and efficiency.
Building Business Intelligence: Supply Chain Analytics Via a Powerful Supply Chain TMS
Tramm, an innovator in supply chain technology, has developed a platform based on the idea that a TMS can only be effective if every aspect of transport management is modeled, integrated, and visible from order inception to final delivery. The end-to-end Tramm TMS platform features route planning and optimization, transporter management, a supply chain control tower, and a powerful mobile app. Comprehensive reporting tools enable strategic planning, and performance analysis and performance management are enhanced via live tempo dashboards, trip scores, and more.
Tramm’s Dashboard Module provides powerful insights built from real-time, integrated external and internal data. Its control tower and visualization module, FleetVision, empowers managers to go from reactive (due to gaps between reported vs. actual performance) to proactive (based on live transportation data). With a better understanding of fleet operations on a granular level, loads are handled more efficiently, freeing up managers to implement performance improvement strategies.
A configurable Order Management module automates order processing, providing detailed visibility into order attributes. Integrated into Tramm TMS for seamless planning and execution, it automatically splits orders based on operational and resource requirements. A client portal allows end customers to capture, manage, and review order status.
Tramm centralizes all supply chain data, improving consistency and accuracy, eliminating discrepancies, and providing a single source of truth. Real-time updates and automated workflows further enhance data reliability, improving decision-making and overall supply chain efficiency.
Three Tactics to Build Business Intelligence through Supply Chain Analytics
To fully leverage the capabilities of a supply chain TMS and enhance business intelligence, companies need to implement specific tactics. Here are three tactics designed to help you achieve these goals, and how Tramm empowers you to do so.
Integrated Supply Chain Analytics
Supply chain analytics need to be woven into every aspect of transportation management. Tramm TMS centralizes data from multiple sources (orders, routes, transporters, etc.), ensuring that critical information is captured and processed in a unified manner.
Tramm eliminates data discrepancies and inconsistencies, creating a reliable, accurate foundation for all decision-making processes. It also provides a comprehensive view of the supply chain, enabling managers to make informed decisions quickly. In addition, internal and external teams have access to the same information, enhancing coordination and cooperation.
Real-Time Data and Insights
Tramm’s TMS and its real-time data processing capabilities allow transport managers to monitor and analyze activities as they happen. Continuous data updates provide a live view from order inception to final delivery, for improved route optimization, tracking, and inventory management.
This capability also allows for proactive identification of bottlenecks and inefficiencies, so managers can quickly implement corrective action and minimize disruptions.
Advanced Reporting and Visualization
Tramm’s supply chain TMS has powerful reporting and visualization tools that turn complex data into actionable insights, helping managers understand and act on key insights effectively.
The platform’s automated reporting on KPIs, such as delivery time, costs, and load utilization, surfaces performance trends and areas for improvement. Tramm’s Dashboard Module translates complex datasets into intuitive graphs, charts, and dashboards to aid decision-making.
Today’s Complex Logistics Call for a Supply Chain TMS That Does More Than Route Shipments
With global freight capacity tightening once again, a volatile market environment, and disruptions the norm, the limited functionality of a legacy TMS isn’t up to the task of managing complex functions across the supply chain.
Tramm TMS leverages the power of advanced analytics, real-time visibility, comprehensive reporting, business intelligence, and performance management tools. With it, organizations can get a better handle on transporter management, improving order flow, optimizing routing, and improving customer satisfaction. To learn how Tramm can transform your supply chain operations, request a demo today.
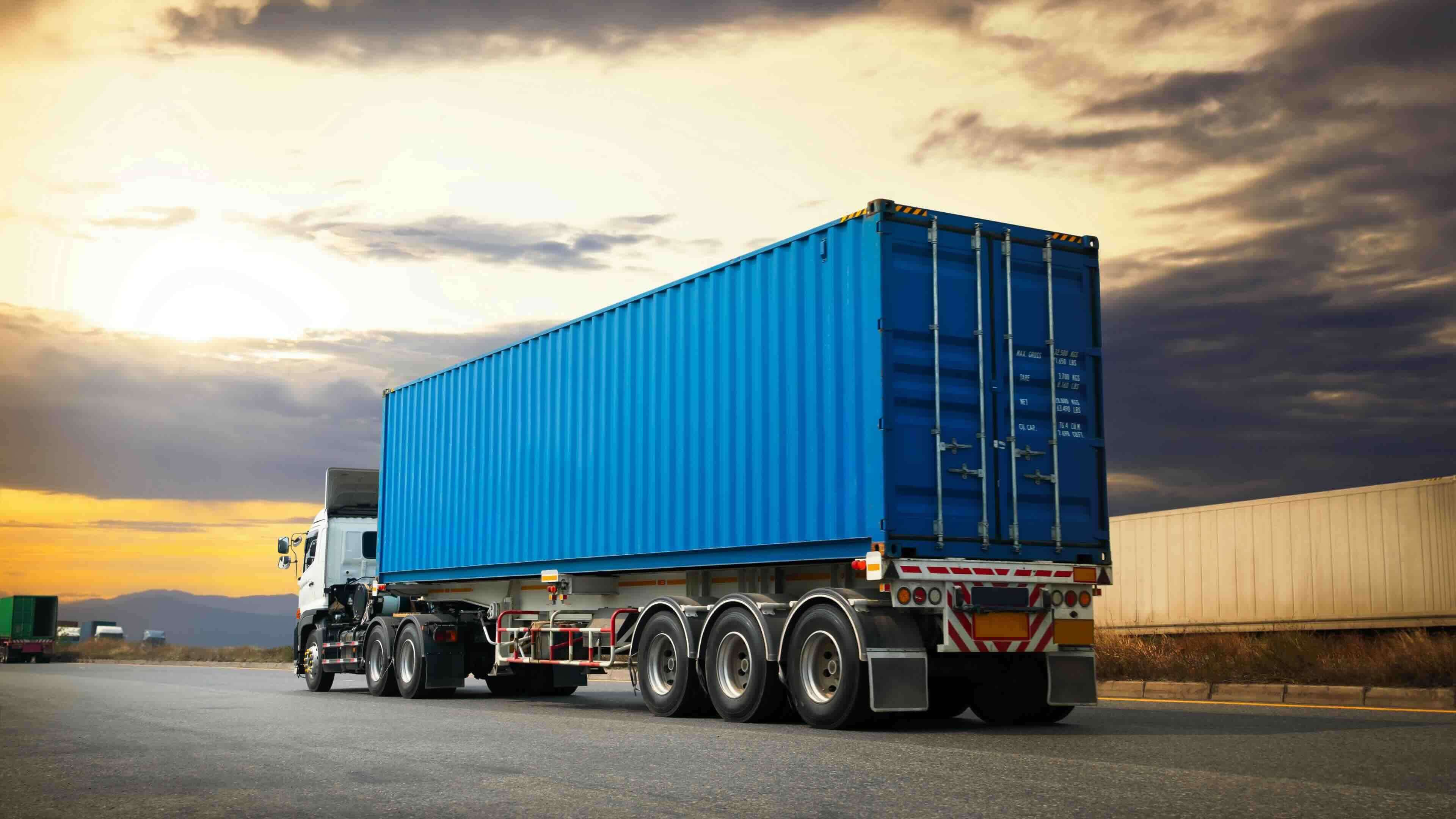