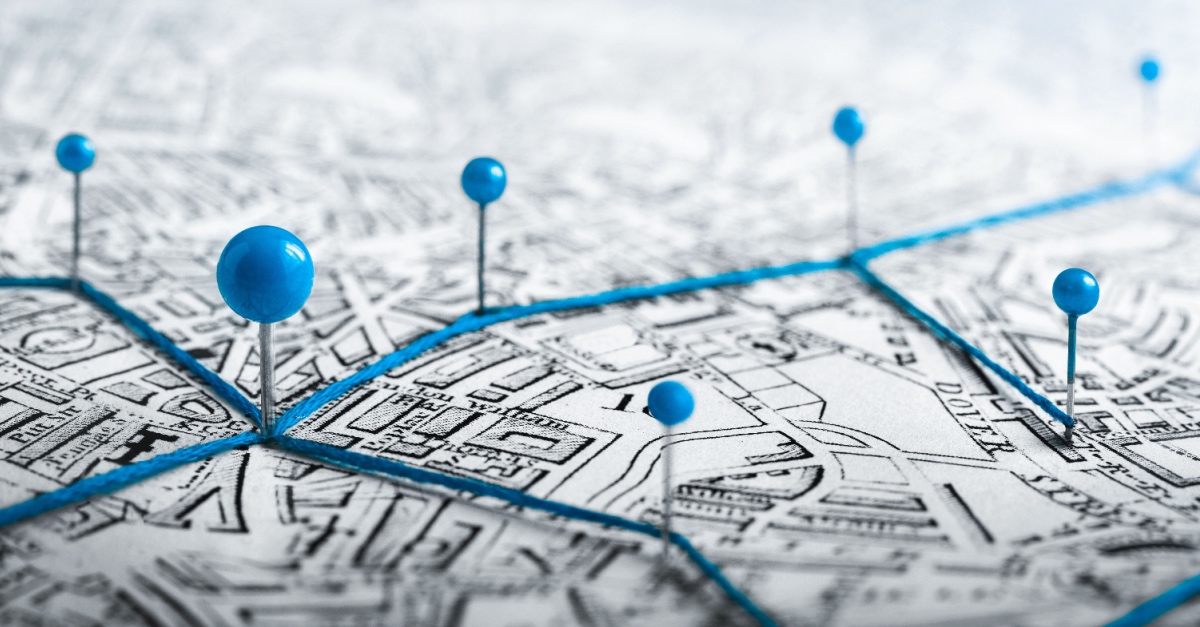
Listen to any quarterly earnings call from major logistics services firms like UPS and FedEx, and you’re bound to hear a plethora of statistics that deal with delivery performance: average miles per delivery stop, stops per route, packages per driver hour, cost per package, on-time delivery rate, etc.
These figures matter a great deal because they help determine the company’s profitability (or loss) that quarter, as indicators of operating performance expressed in KPIs. They also have a great deal to do with the concept of route optimization, the art and science of executing deliveries as efficiently as possible.
Within the broader scope of logistics planning – coordinating the movement, storage, and flow of goods within a supply chain – route optimization plays a key role. Transportation managers put a great deal of effort into reducing total miles, eliminating delays, and improving route density metrics (number of stops, packages per stop, per driver, etc.). Performance goals include higher on-time rates, lower operating costs, and higher customer satisfaction, among other key business objectives.
We’ll take a closer look at route optimization, why it matters, how it’s achieved, and the technology behind it.
Aspects of Route Optimization
In logistics and transportation, whether truckloads from a plant to a distribution center or stepvans from a hub to a local run, route optimization involves finding the most efficient travel paths. Factors include the distance between points, traffic patterns, delivery windows, fuel costs, and vehicle capacity.
Determining the best fleet to use in each case is also an important success factor. Transportation managers must not only select between different vehicle types and sizes for each set of deliveries, but also the right number of each type based on fixed and variable costs. Fixed costs include driver salaries and wages, vehicle leasing or depreciation, insurance, licensing and permits, and administrative costs. Variable costs include fuel, driver overtime, maintenance and repairs, tolls, loading and unloading, and third-party fees when using a logistics provider.
In addition to vehicle type and size, other route optimization variables include product suitability and restrictions (i.e., refrigerated), road networks, customer time windows, backhaul opportunities, driver hours of service (HOS), efficient load building, and fuel/rest stop planning.
Balancing fixed and variable costs is important because it helps achieve route optimization by minimizing the total cost per delivery while maintaining efficiency and delivery schedules. By selecting the right number of vehicles, adjusting for stop density, and optimizing distances, businesses can achieve substantial savings and performance gains.
Why Route Optimization is Crucial
Through route optimization businesses can achieve greater cost efficiency, improve delivery performance, and foster sustainability. By identifying the most efficient travel routes, they can minimize fuel consumption, lower labor costs, and reduce vehicle wear and tear. This is particularly important in a competitive environment where even small cost savings can spell the difference between a division’s profit and loss.
Optimized routing helps ensure timely deliveries, improving service reliability and customer satisfaction. From an environmental perspective, it means reduced fuel usage and lower carbon emissions, supporting sustainability initiatives and regulatory compliance. This is also something that can resonate with customers who value greener transportation.
Route optimization also helps companies maximize resource utilization through increased efficiency of vehicle, driver, and asset usage. By balancing fleet capacity, stop density, and delivery schedules, transportation managers can reduce empty miles and truck idling. The result: more streamlined operations, better use of resources, and improved performance.
Logistics Challenges Affecting Route Optimization
It’s hard to believe given technological advances across logistics functions, but manual route planning is still widespread, especially among small to mid-sized businesses. Many companies continue to rely on a combination of spreadsheets, paper maps, or simple routing tools for delivery and route planning. These methods are often in use when delivery volume is manageable and the network is relatively small. But they are inefficient, lack scalability, increase costs and risk customer dissatisfaction.
As supply chains become more complex and expectations increase, the use of route optimization software is growing. Advanced tools like transportation management systems (TMS), GPS tools, and AI are becoming much more common. They all leverage real-time data, machine learning and predictive analytics to optimize routes based on factors such as traffic, weather, fuel costs, and delivery windows.
Larger enterprises – both logistics providers and shippers – rely heavily on advanced route optimization technology to manage vast delivery networks. As e-commerce growth and customer expectations rise, more companies are shifting toward automated solutions to stay competitive and improve operational efficiency.
The Role of Technology
Technology has revolutionized route optimization, enabling businesses to streamline logistics and reduce costs. Route optimization software integrates GPS, telematics, and algorithms, analyzing real-time and historical data to create the most efficient travel paths. These tools consider variables like traffic patterns, weather, delivery time windows, and vehicle capacity.
AI and machine learning enhance these capabilities with predictive analytics, looking at traffic trends, fuel costs, and customer demand to anticipate delays and proactively recommend adjustments. Machine learning models continuously refine routing strategies by analyzing historical data, improving accuracy and adaptability.
By integrating these technologies into logistics planning, companies can reduce total miles driven, minimize delays, and optimize resource use. This helps them achieve their key goals (cost savings, higher on-time delivery rates, improved customer satisfaction).
Key Features of Route Optimization Software
Route optimization software gives logistics managers an advanced tool for improving efficiency and reducing costs. A key feature is vehicle selection. When the optimal vehicle is chosen for each route based on capacity, cost, and suitability, it maximizes utilization and reduces costs. Dynamic route adjustments allow for real-time updates based on changing traffic, weather conditions, or unexpected delays, helping maintain on-time performance.
Multi-stop optimization efficiently sequences stops for deliveries, reducing total miles driven and improving route density. Beyond basic stop sequencing, route optimization software should be designed to handle the complexity, nuances and business rules of each company. This could include factoring things like load building based on relative item weight, customer delivery windows, and site restrictions, to optimize stop sequencing.
System integration ensures seamless communication with WMS, TMS, and fleet management systems (FMS), providing end-to-end visibility across functional areas. And driver behavior analytics enhance efficiency and safety by monitoring factors such as speed, braking patterns, and fuel consumption.
Best Practices for Implementation
Successfully implementing route optimization software requires a strategic approach. Start by defining clear objectives that align with your business goals. This includes identifying key metrics such as cost savings, delivery speed, or carbon emissions reduction in order to measure success effectively.
Invest in scalable technology that can grow with your business. As you expand or deal with demand spikes, the solution should be able to adapt to meet changing demands without disrupting workflows.
Provide thorough training in order to maximize the benefits of routing tools. A well-trained workforce leads to better decision-making and greater efficiency.
Prioritize continuous monitoring and adjustment. Real-time analytics can identify inefficiencies, respond to changing conditions, and fine-tune processes. Regular reviews ensure the system continues to deliver value over time and adapts to evolving challenges.
Partnering with the Right Technology Provider
Key characteristics to look for include proven expertise in logistics software and analytics, as well as an understanding of your industry's specific needs. Scalability is another important requirement, future-proofing the technology so it can grow with your business and adapt to changing needs. The ability to provide seamless integration via API or EDI with WMS, TMS, and FMS sets up real-time data sharing and better collaboration across the supply chain.
The right provider should be able to deliver a realistic implementation timeline that factors in data readiness, integration complexity, user training and any customization. For SMBs with fewer requirements, it can happen in a matter of weeks; in more complex enterprise scenarios it can take 3-6 months, often in a phased rollout.
Continuous updates ensure the technology stays on track with advances in AI, machine learning, and predictive analytics. The provider should also be able to deliver a tailored solution that addresses your unique requirements. This will help optimize performance, increase efficiency and cost savings, and improve delivery speed and accuracy, delighting customers and building loyalty.
A Tech-Driven Route To Greater Transport Efficiency
Route optimization has become a cornerstone of supply chain management, and a reliance on outdated manual processes falls woefully short of achieving its goals. Through advanced technology, businesses can become more efficient, save on costs, and improve customer satisfaction and sustainability.
Tramm, an innovator in supply chain technology, has developed a cloud-based end-to-end TMS platform that combines route planning and load building, transporter management, order management, a logistics control tower, and a mobile app. With this approach, Tramm has solved the problem of fragmented supply chain systems, integrating key functions into a unified, scalable system.
Tramm’s Planning and Optimization Module leverages powerful algorithms to handle complex routing environments, accounting for variables that accurately reflect on-the-ground transport operations. Its dynamic multi-day route planning handles scheduling for primary, secondary, and service-based fleets. Users can easily make real-time adjustments based on changing needs, including “what if” visualization and scenarios. A load builder/stackability app automatically plans loads that are tightly synced with capacity and route optimization.
To find out how Tramm’s unified approach can drive transportation efficiency and cost savings while helping you realize sustainability goals, request a demo today.
Related Resources
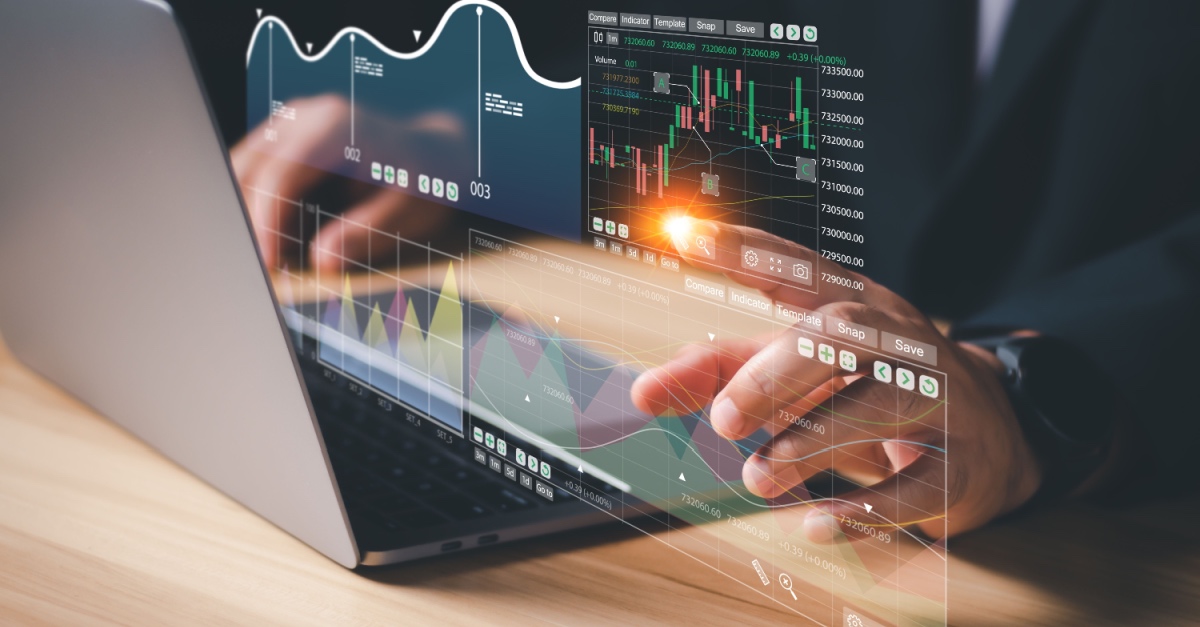
Smarter Shipping: Leveraging a Supply Chain TMS for Enhanced Business Intelligence
As we’re not yet living in the age of “Star Trek,” where people and things can be transported by breaking down and then reassembling molecules thousands of miles away (Elon Musk: take note), we here on Earth still count on shipping and logistics. By land, sea, and air, massive amounts of cargo are moved every day to keep global commerce humming. And a modern supply chain TMS (transportation management system) is a key technology that helps make it happen more efficiently.
Intelligent shipping combines business intelligence, planning, and execution tools, along with strategy and process, to optimize routing, scheduling, loading, communication, transporter management, etc. There are many primary and secondary benefits, including faster, more accurate deliveries, cost savings, improved customer satisfaction, better driver engagement and retention, and improved inventory management and demand forecasting.
A true supply chain TMS can help you achieve your goal of intelligent shipping by enhancing business intelligence and optimizing all aspects of logistics and transportation.
The Role of Supply Chain Analytics in Global Transport Operations
Supply chain analytics help organizations both keep track of and improve operational performance across various interdependent functions. All of that activity is throwing off tons of data, requiring sophisticated systems to synthesize and analyze, produce insights, and make recommendations. Increasingly, this is done by automating what had been manual processes, such as demand forecasting and route optimization.
The capabilities of supply chain data analytics have advanced significantly in recent years, increasing operational efficiency across all phases of transportation and logistics. For example, modern systems can assess risks associated with everything from geopolitical disruptions and natural disasters to freight capacity and supplier performance. Companies can then develop contingency plans and make better-informed decisions to mitigate these risks.
An advanced supply chain TMS can track KPIs such as the percentage of on-time deliveries, delivery error rate, cost per mile and cost per unit, load utilization percentage, average delivery time, and order cycle time. All of these metrics act as a barometer of business performance and efficiency.
Building Business Intelligence: Supply Chain Analytics Via a Powerful Supply Chain TMS
Tramm, an innovator in supply chain technology, has developed a platform based on the idea that a TMS can only be effective if every aspect of transport management is modeled, integrated, and visible from order inception to final delivery. The end-to-end Tramm TMS platform features route planning and optimization, transporter management, a supply chain control tower, and a powerful mobile app. Comprehensive reporting tools enable strategic planning, and performance analysis and performance management are enhanced via live tempo dashboards, trip scores, and more.
Tramm’s Dashboard Module provides powerful insights built from real-time, integrated external and internal data. Its control tower and visualization module, FleetVision, empowers managers to go from reactive (due to gaps between reported vs. actual performance) to proactive (based on live transportation data). With a better understanding of fleet operations on a granular level, loads are handled more efficiently, freeing up managers to implement performance improvement strategies.
A configurable Order Management module automates order processing, providing detailed visibility into order attributes. Integrated into Tramm TMS for seamless planning and execution, it automatically splits orders based on operational and resource requirements. A client portal allows end customers to capture, manage, and review order status.
Tramm centralizes all supply chain data, improving consistency and accuracy, eliminating discrepancies, and providing a single source of truth. Real-time updates and automated workflows further enhance data reliability, improving decision-making and overall supply chain efficiency.
Three Tactics to Build Business Intelligence through Supply Chain Analytics
To fully leverage the capabilities of a supply chain TMS and enhance business intelligence, companies need to implement specific tactics. Here are three tactics designed to help you achieve these goals, and how Tramm empowers you to do so.
Integrated Supply Chain Analytics
Supply chain analytics need to be woven into every aspect of transportation management. Tramm TMS centralizes data from multiple sources (orders, routes, transporters, etc.), ensuring that critical information is captured and processed in a unified manner.
Tramm eliminates data discrepancies and inconsistencies, creating a reliable, accurate foundation for all decision-making processes. It also provides a comprehensive view of the supply chain, enabling managers to make informed decisions quickly. In addition, internal and external teams have access to the same information, enhancing coordination and cooperation.
Real-Time Data and Insights
Tramm’s TMS and its real-time data processing capabilities allow transport managers to monitor and analyze activities as they happen. Continuous data updates provide a live view from order inception to final delivery, for improved route optimization, tracking, and inventory management.
This capability also allows for proactive identification of bottlenecks and inefficiencies, so managers can quickly implement corrective action and minimize disruptions.
Advanced Reporting and Visualization
Tramm’s supply chain TMS has powerful reporting and visualization tools that turn complex data into actionable insights, helping managers understand and act on key insights effectively.
The platform’s automated reporting on KPIs, such as delivery time, costs, and load utilization, surfaces performance trends and areas for improvement. Tramm’s Dashboard Module translates complex datasets into intuitive graphs, charts, and dashboards to aid decision-making.
Today’s Complex Logistics Call for a Supply Chain TMS That Does More Than Route Shipments
With global freight capacity tightening once again, a volatile market environment, and disruptions the norm, the limited functionality of a legacy TMS isn’t up to the task of managing complex functions across the supply chain.
Tramm TMS leverages the power of advanced analytics, real-time visibility, comprehensive reporting, business intelligence, and performance management tools. With it, organizations can get a better handle on transporter management, improving order flow, optimizing routing, and improving customer satisfaction. To learn how Tramm can transform your supply chain operations, request a demo today.
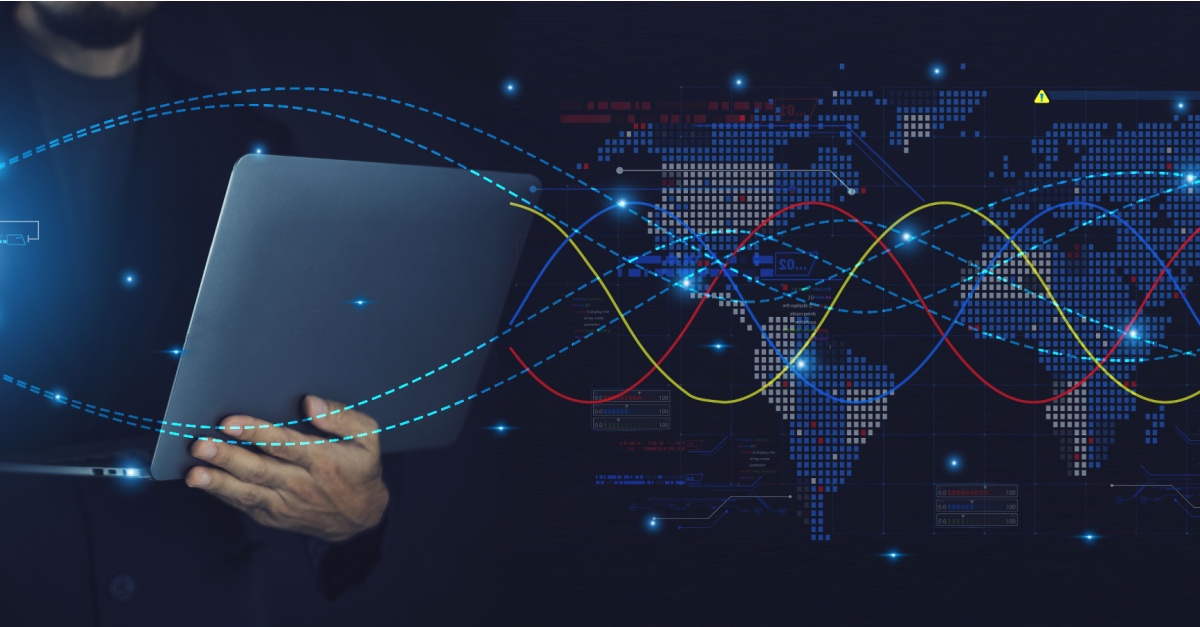
Improving Strategic Decision-Making in Logistics With Advanced Analytics
Years back, UPS had a catchy marketing tagline that said, “We Love Logistics.” Well, given the complexity and increasing demands on logistics and supply chain teams, you had better love it, as it’s a highly demanding discipline. This is why decision-making in logistics needs advanced analytics backup: There’s little margin for error when contracts and valuable customer relationships are riding along with each delivery.
Advanced analytics are, in fact, transforming logistics processes in everything from route optimization to driver hours of service, dispatch and delivery, transporter selection, and even yard management. Among the many benefits of this kind of digital approach are greater operational efficiency, lower costs, and improved customer satisfaction.
The Role of Advanced Analytics in Strategic Logistics Decisions
Advanced analytics uses sophisticated techniques and tools to analyze data, uncover deep insights, predict trends, and improve decision-making. It goes beyond simple descriptive analytics or a summary of historical data, using methods that provide actionable outputs and strategic guidance.
Predictive analytics, as the name implies, involves using statistical models and machine learning algorithms to forecast future outcomes based on patterns in historical data. The next step beyond that is prescriptive analytics, which recommends specific actions to achieve desired outcomes through analysis of potential scenarios and their implications.
Helping power decision-making in logistics, control towers have risen in importance as a way to manage the complex flow of inbound/outbound assets, loads, and team members. Primarily, it’s a centralized hub that provides end-to-end visibility, real-time monitoring, and coordination of supply chain activities. Logistics managers access a control tower to track shipments, manage exceptions, and make data-driven decisions geared toward optimized operations.
How Analytics Lead To Better Logistics Decision-Making
Advanced analytics plays a transformative role in optimizing transportation and delivery. Here are specific examples that highlight its impact:
Route Optimization
Real-time analytics assess traffic patterns, weather conditions, and fuel costs, as well as factors like delivery windows and vehicle/site/production restrictions, to determine the most efficient routes. For example, a transporter uses GPS-enabled analytics to avoid congested roads, helping speed up delivery and reduce fuel costs.
Route optimization tools leverage advanced algorithms to improve load planning and cross-docking. They can also optimize planning for multi-modal transportation (LTL and FTL, box trucks and sprinter vans for last mile, etc.), multi-day, and multi-fleet scenarios.
ETA Predictions and Updates
Analytics integrates real-time tracking and other telematics data and compares it with planned data and historical patterns to provide accurate delivery ETAs. Transporters and couriers use advanced analytical models to provide updates on delays due to traffic or bad weather, improving transparency and satisfaction.
Evaluating Transporter, Fleet Performance
Advanced analytics help assess and improve both transporter and fleet performance. By tracking key metrics such as on-time delivery rates, claims for damaged goods, and cost efficiency, shippers gain valuable insights into transporter reliability and efficiency. These metrics help identify high-performing carriers and drivers, enabling shippers to negotiate favorable contracts and foster long-term partnerships.
For fleet drivers, analytics can evaluate metrics on adherence to schedules, fuel efficiency, safety records, and driving behaviors like braking or speeding. This helps maintain high standards while identifying areas for training or improvement.
Integrated analytics can also consolidate data across all third-party and fleet operations. This helps shippers optimize fleet utilization, balance workloads, and replace underperforming drivers or carriers, enhancing supply chain's performance and reliability.
Shipment Consolidation and Load Optimization
Data models analyze shipment volumes and destinations to maximize cube utilization and reduce the number of trips. Logistics providers can use this advanced modeling to consolidate LCL freight from multiple shippers heading to the place, lowering operating costs and simplifying scheduling.
Best Practices for Implementing Analytics in Logistics
Successfully integrating analytics into logistics operations requires strategic alignment and thoughtful execution. Start by fostering a data-driven culture. All teams, from operations to management, must understand the value of analytical decision-making. This kind of mindset shift is essential for embracing data analytics as a core part of the logistics workflow.
Invest in integrated technology to streamline data flow and visibility. Combining analytical tools with assets like a Transportation Management System (TMS), a Warehouse Management System (WMS), and a logistics control tower contributes to greater efficiency by consolidating multi-source data. Integrating these complementary systems in a logistics tech stack facilitates seamless communication and better analytical outcomes.
Prioritize quality, real-time data to enable responsive decision-making. Determine what kind of data you need and how often you need it. Do you need weekly or daily logistics reports, or do you need up-to-date information every time you log into the dashboard? Access to real-time data analytics lets you monitor and analyze trends over time, allowing you to better respond to opportunities and eliminate inefficiencies.
Better Decision-Making in Logistics, Fueled By Advanced Analytics
Analytics are transforming logistics by enabling data-driven decisions that improve efficiency and customer satisfaction. Predictive and prescriptive analytics help forecast trends and recommend strategies to address challenges such as route optimization, transporter selection, and improving on-time performance.
A logistics control tower offers comprehensive, real-time visibility into logistics and supply chain activities. Integrating it with TMS and WMS, overlaid with analytics, helps logistics teams reduce costs and respond faster to disruptions and market shifts.
Tramm, an innovator in supply chain technology, has developed an end-to-end TMS platform that combines order management, route planning and load building, transporter management, a logistics control tower, and a powerful mobile app. With this comprehensive approach, Tramm has solved the problem of fragmented supply chain systems by integrating key functions into a unified, scalable platform. Tramm’s business intelligence tools increase performance at the fleet and driver level by empowering data-driven decision-making.
To find out how Tramm’s unified platform and advanced analytics can help you drive transportation efficiency and improve decision-making in logistics, request a demo today.
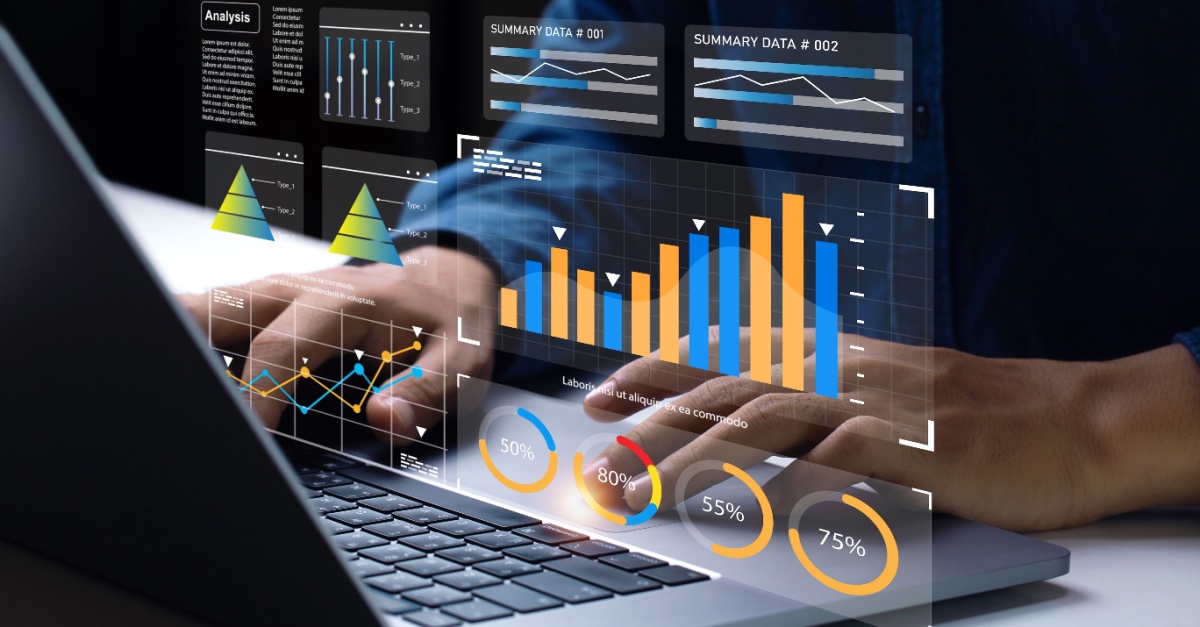
The Importance of Detailed Order Data in Supply Chain Optimization
As supply chains become increasingly complex, the demand for efficiency and flexibility has never been greater as companies struggle to meet rising customer expectations and deal with global disruptions. Having detailed order data is one key ingredient in supply chain optimization, enabling better decision-making, improved efficiency, and reduced costs.
The ability to access and analyze clean, accurate data improves demand forecasting, inventory management, and fulfillment operations by providing greater visibility into SKU levels and order status. It also helps streamline transportation, reduce lead times, and optimize carrier selection.
Conversely, a lack of detailed order data leads to a variety of negative consequences. These include mismanaged inventory (more stockouts, overstocks), fulfillment delays, disrupted workflows, inaccurate demand forecasts (over or underproduction), strained customer relationships, and financial impacts.
This is why order data accuracy is critical in supply chain optimization. It improves decision-making, enhances efficiency, and reduces costs.
Understanding Order Data’s Role in Supply Chain Optimization
Order data includes information on products, quantities, prices, customer preferences, delivery schedules, and fulfillment status. Sources of order data include order management systems (OMS), enterprise resource planning (ERP, often the central hub), customer relationship management (CRM), procurement systems, and, if there’s a retail component, point-of-sale (POS) systems.
Detailed order data is the foundation for optimizing inventory management, transportation and delivery, warehousing, and fulfillment — in short, every operational aspect of the business.
An inability to control how orders are handled from inception contributes to poor decisions, and inaccurate data is often the culprit. The lack of a unified, efficient system for moving orders from planning to execution and doesn’t enable real-time visibility is a recipe for disaster. The result is a limited ability to represent actual order status in a meaningful way.
Enhancing Demand Forecasting and Inventory Management
A business’s success or failure is inextricably linked to its ability to accurately forecast demand and, from there, properly manage inventory levels. Detailed order data (current and historical), as well as factors like market trends and customer feedback, allow businesses to predict demand more accurately and optimize inventory levels.
Using manual processes to handle order data, even in small-to-medium businesses, is a system rife with errors and inaccuracies. The ability to access real-time order data informs smarter reordering and replenishment strategies. This helps reduce overstocks or out-of-stocks by leveraging actual demand patterns, maintaining cash flow, reducing carrying costs, and keeping customers happy.
Improving Order Fulfillment and Reducing Lead Times
Having detailed order data helps minimize fulfillment errors by optimizing picking, packing, and shipping processes. By accurately tracking customer demand, businesses can expedite order processing and optimize transportation routes to reduce lead times.
Order allocation can be fine-tuned based on stock availability and proximity to customers, enabling faster, more efficient fulfillment. This not only speeds up deliveries but also improves customer satisfaction.
Optimizing Transportation and Logistics
Another benefit of having detailed, accurate order data is on the logistics side. With it, businesses can optimize order routing, consolidate shipments, and reduce delivery costs. They can also choose the most cost-effective carriers and shipping methods based on order data.
Order consolidation involves centralizing items from multiple orders into a single location or by combining multiple orders from different sales channels into a single system. This helps lower transportation costs, improve inventory management, simplify logistics, and provide a better customer experience by reducing split shipments.
With the ability to access and analyze detailed order data, businesses can save by taking advantage of bulk shipping discounts, optimizing carrier selection, and avoiding last-minute changes in shipping schedules.
Supporting Customer Satisfaction and Personalization
Detailed order data allows businesses to track customer preferences, providing personalized offerings and recommendations. It also improves proactive communication, informing customers about order status, estimated delivery times, and potential delays.
This type of transparency enhances trust and helps companies to manage customer expectations. It contributes to a consistently excellent customer experience, boosting satisfaction scores, repeat business, and brand loyalty.
Without Detailed Order Data, Things Break Down
Detailed order data is critical for supply chain optimization, enabling better demand forecasting, more efficient inventory management, and faster fulfillment. It allows businesses to streamline transportation, optimize routing, and reduce delivery costs. Accurate order data also supports customer satisfaction by providing real-time order status and personalized offerings, reducing errors and improving efficiency. A lack of such data, for instance, due to manual processes or outdated software, leads to fulfillment delays, inventory mismanagement, and strained operations.
Tramm, a developer of a leading unified supply chain management platform, combines a powerful OMS within its transportation management system (TMS) suite. This integrated approach provides end-to-end visibility and control over order fulfillment and shipping processes. Tramm’s Order Management Module ensures that orders are fully consolidated before being released for shipment, while the TMS manages transportation in the most efficient, cost-effective manner.
The power of Tramm lies in its ability to optimize the entire process from order management through planning and route optimization, contract management, fleet management, and performance analytics. A versatile driver app provides workflow management, electronic proof of delivery, compliance tracking, and auditing.
Request a demo today to learn more about how Tramm can drive supply chain optimization through its cutting-edge tools and holistic approach.
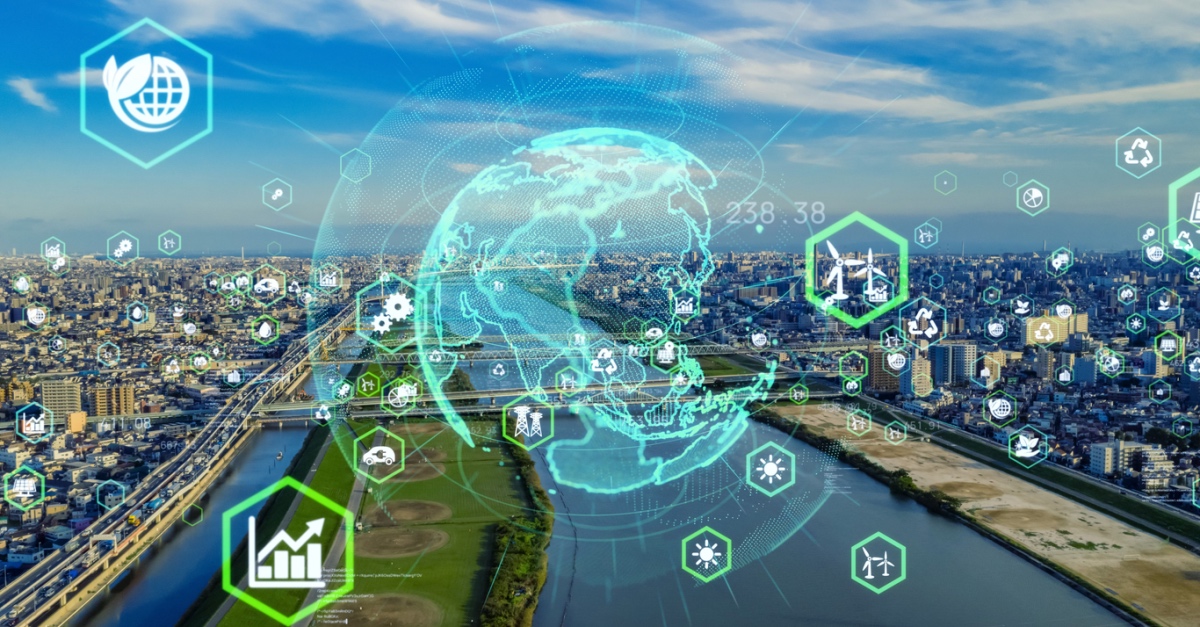
Sustainable Logistics: How Optimized Routing Can Reduce Your Carbon Footprint
The world of logistics and transportation cannot afford to slow down, and the trend toward sustainable logistics is working hard to catch up. Demand for shipping and delivery services is only increasing in a fast-moving, interconnected global economy. But with this growth comes greater pollution levels from vehicles and logistics networks.
For this reason, it shouldn’t be surprising that 75% of logistics companies have a focus on sustainability, according to a May 2024 survey by the Germany-based Logistics Hall of Fame. A majority of respondents rated the risk of financial loss due to climate change as “medium to high.”
This is why major efforts are underway to reduce trucking-generated pollution by implementing a sustainable logistics program. These include efforts to optimize routing, grow alternative fuel fleets, increase the use of automation, enforce stricter emissions standards, and ramp up intermodal transportation.
Optimized routing, in particular, has emerged as a powerful tool to not only reduce transportation costs but also significantly minimize carbon emissions, making logistics operations more sustainable.
The Environmental Impact of Logistics
Transportation contributes more than a third of all CO2 emissions globally, with nearly two-thirds of that coming from trucking, according to the International Energy Agency (IEA). In addition, transportation relies on petroleum products for nearly 91% of its energy, down just 3.5 percentage points from the early 1970s.
Excessive fuel usage in everything from long-haul trucking to last-mile delivery, traffic congestion, and poorly planned routes contribute to higher CO2 emissions. At the same time, regulatory pressure and consumer demand for more sustainable business practices are forcing companies to adapt.
The Basics of Route Optimization
Route optimization tools use advanced algorithms and predictive analytics, parsing historical and real-time data to identify the most efficient delivery routes. Factors taken into account include traffic conditions, weather, vehicle capacity, delivery windows, and road restrictions.
Many routing tools within a transportation management system (TMS) also include load optimization capabilities, enabling companies to maximize their available freight capacity and improve key metrics like revenue per mile, cost per delivery, and fleet utilization.
State-of-the-art route optimization tools employ dynamic multi-day route planning and scheduling across trucking modes, everything from LTL, TL, middle mile, last mile, private fleet and dedicated transportation services.
Reducing Fuel Consumption and Carbon Emissions
As route optimization enables companies to reduce the number of miles driven, an immediate, tangible benefit is a significant saving on fuel consumption.
These tools also allow drivers to avoid areas of traffic congestion, helping to improve on-time delivery performance. This not only reduces truck dwell time and, thus, tailpipe emissions, but also increases customer satisfaction.
By optimizing load capacity, companies can put fewer trucks on the road, further reducing fuel usage and emissions — further driving sustainable logistics.
The Role of Real-Time Data in Sustainable Routing
Access to real-time data on traffic, weather, and road conditions allows for dynamic rerouting to avoid delays and minimize emissions. Traffic data can come from GPS systems and platforms like Google Maps or Waze for information on congestion, accidents, and road closures.
Weather data from apps like The Weather Channel or OpenWeatherMap provide updates on conditions (thunderstorms, high wind, fog, snow) that might affect a trip, rerouting if necessary. Telematics and sensors take in data on vehicle location, speed, fuel usage, and status from onboard systems or fleet management software.
Updates from order management systems (OMS) on delivery windows and customer availability also become part of the routing equation, as does data on weight or height restrictions and road closures from transportation departments. Routing software also tracks fuel efficiency and vehicle performance, reducing environmental impact.
Other Benefits of Route Optimization
In addition to reduced fuel consumption and lower operating costs, route optimization enables faster, more reliable deliveries, improving customer relationships and fostering loyalty.
Optimized routing also helps companies meet their environmental goals through sustainable logistics. This includes compliance with government regulations and qualification for certifications such as LEED, ISO14001, and SmartWay.
Route Smarter, Stay Greener
Route optimization improves logistics efficiency and plays a crucial role in reducing carbon emissions. An investment in this technology helps drive both sustainability and competitiveness in a business climate that increasingly values environmental responsibility. By embracing sustainable logistics practices through the use of these tools, companies can reach their goals while driving down costs through efficiency gains.
Tramm, an innovator in supply chain technology, has developed an end-to-end TMS platform that combines route planning, load building, transporter management, a supply chain control tower, and a powerful mobile app. With this end-to-end approach, Tramm has solved the problem of fragmented supply chain systems by integrating key functions into a unified, scalable platform.
Tramm’s Planning and Optimization Module handles complex routing environments, accounting for variables such as rules and constraints that accurately reflect on-the-ground transport operations. It allows users to easily adapt their plans based on changing needs, including “what if” visualization and scenarios that enable real-time adjustments. A load builder/stackability app lets them automatically plan loads that are tightly synced with capacity and route optimization.
To find out how Tramm’s unified approach can drive transportation efficiency and cost savings while helping you realize sustainability goals, request a demo today.
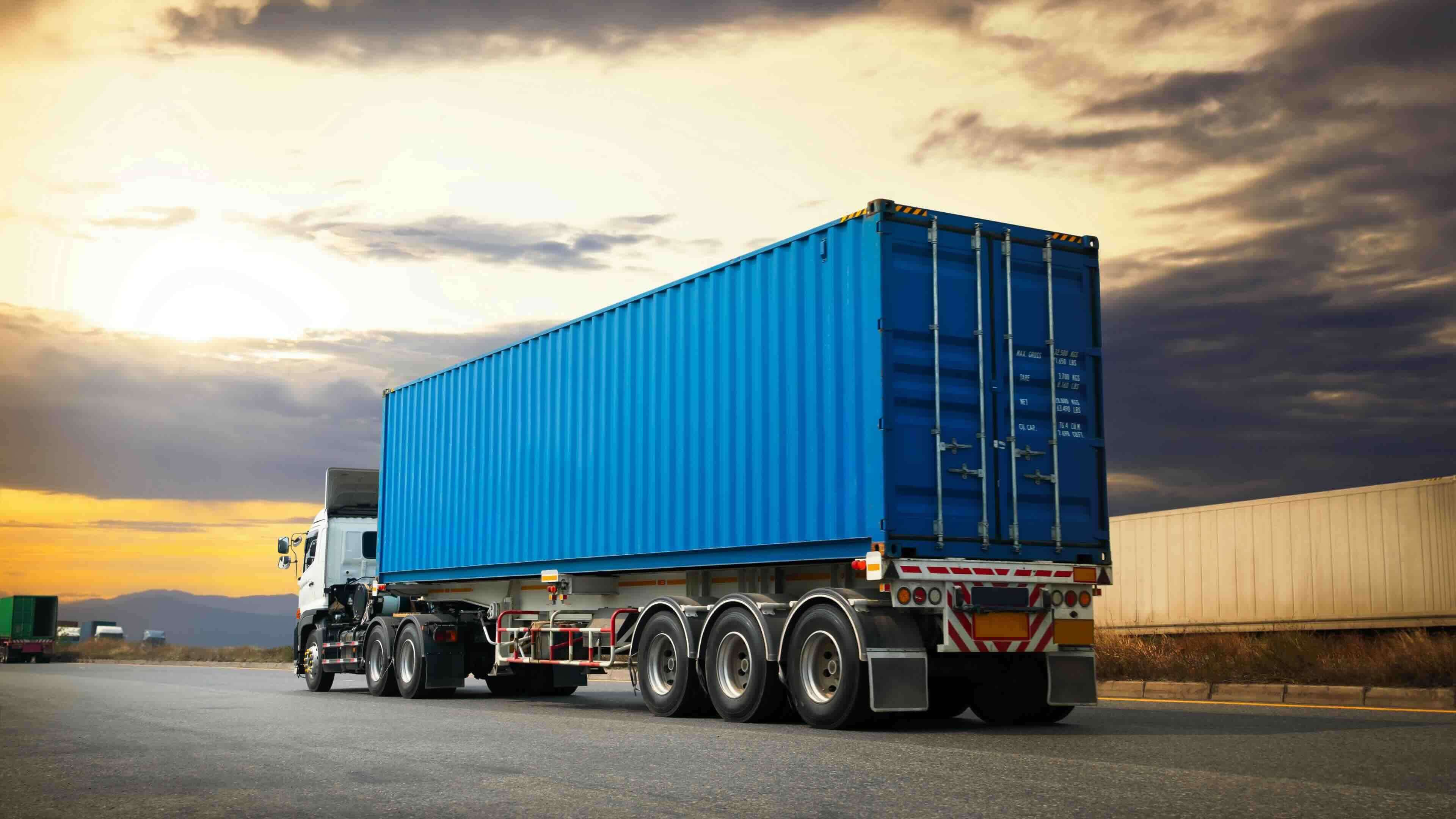