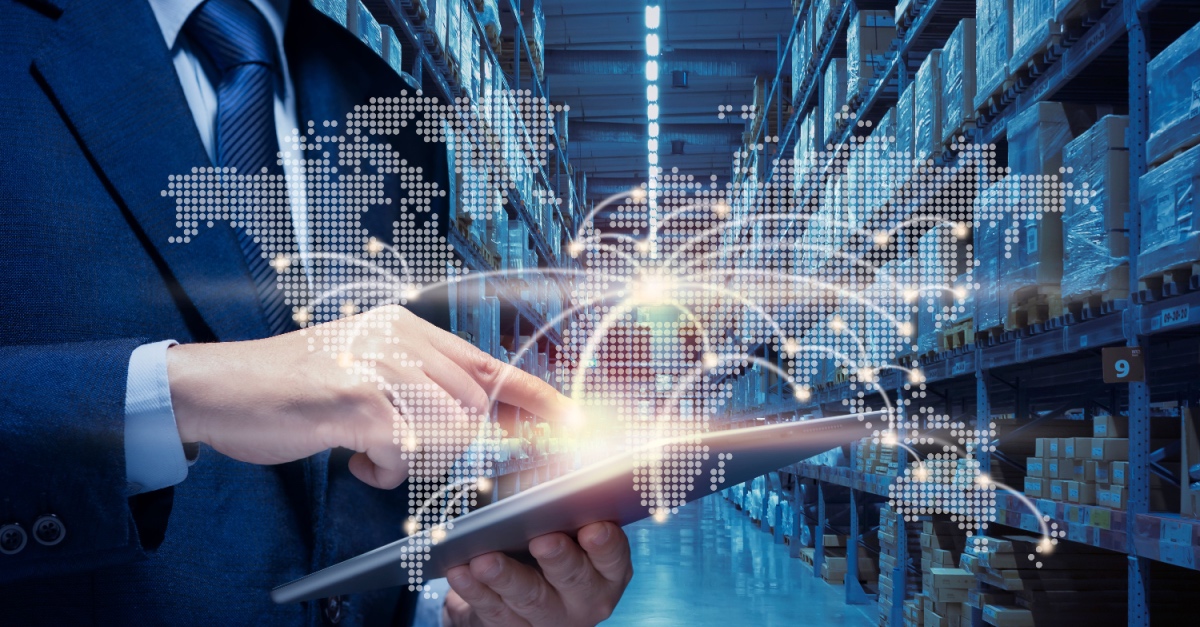
Saying “logistics are complex” may be akin to saying “water is wet,” but the level only seems to be rising. Companies are expanding sales channels, trading partners, vendors, and markets as they seek new opportunities, and each step adds a layer of complexity. In the process, they often pursue a point solution approach, creating a patchwork of technologies that require a heavy IT lift in terms of integration and maintenance.
A logistics management system (LMS, not to be confused with a labor management system) is a technology solution that addresses this issue. It’s a software tool that helps companies manage the flow of goods from production to end customers.
An LMS can help improve efficiency, reduce costs, and provide a better customer experience. It does this by consolidating all logistics operations into one integrated platform. A truly unified LMS can help shippers reduce complexity and improve supply chain resiliency. By coordinating multiple logistics functions within a single system, an LMS eliminates silos and promotes real-time collaboration.
What is a Unified Logistics Management System?
A unified LMS integrates various logistics functions, such as inventory, transportation, and warehouse management. Key features include access to real-time data, automated processes, and end-to-end visibility. By consolidating logistics operations, a unified LMS removes inefficiencies that naturally arise from disparate technologies. The result is improved decision-making and better demand forecasting.
Unification is critical for managing complex, multi-node supply chains under pressure from heightened customer expectations, geopolitical and labor tensions, fluctuating markets, and global sourcing. A unified LMS provides the flexibility and scalability to adapt to new business challenges and opportunities, increasing responsiveness and competitiveness.
The Operational Complexity of Logistics
Managing the flow of goods from origin to customer involves many moving parts. Disparate systems and silos, as noted above, slow down operations and drive inefficiency. This often requires manual intervention to reconcile data across platforms, resulting in errors and delays.
Reliance on manual workflows adds to the operational burden, lowering productivity and increasing the risk of errors. Inventory management, shipping, tracking, and reporting are time-consuming and require coordination across departments, making it difficult to maintain accuracy and efficiency.
The sheer volume of data generated in logistics — customer orders, inventory updates, shipping schedules, etc. — can quickly overwhelm traditional systems. Handling this information load without the proper infrastructure increases complexity and response times, impacting overall supply chain performance.
A Unified LMS: Reducing Operational Complexity
Imagine a centralized platform where all logistics data is stored, providing real-time visibility across operations. This would remove the need to constantly reconcile data across multiple systems. Tracking orders, monitoring shipments, and accessing up-to-date inventory levels would become easier. Real-time data access would also allow logistics managers to make faster, more informed decisions that improve supply chain efficiency.
This type of consolidation reduces errors and eliminates delays caused by manual data entry. Teams no longer need to cross-check information across systems; all stakeholders can access the same accurate data. Greater visibility streamlines coordination among suppliers, warehouse managers, transporters, and customers, leading to faster response times and fewer disruptions.
Streamlining Communication and Collaboration
A unified LMS also enhances internal and external communication by eliminating data silos. This makes it easier to track orders, manage inventory, and resolve issues in real time.
With all logistics operations accessible on a single platform, teams can collaborate more effectively, reduce communication barriers, and increase alignment. This level of coordination improves performance, so every aspect of the logistics process runs smoothly and efficiently.
Workflow Automation
Automating orders, inventory updates, and shipment tracking reduces the need for manual intervention. Automated workflows also help eliminate errors and streamline administrative tasks, freeing up logistics teams to focus on more high-level, strategic activities.
For example, an automated system can trigger the creation of shipping labels, inventory adjustments, and confirmations upon order placement. This ensures that everything is processed rapidly without requiring additional input. Automation helps companies reduce lead times, improve accuracy, and reduce errors in orders and shipping.
Integrated Inventory and Transportation Management
A unified LMS combines inventory and transportation data, optimizing routing while making order fulfillment faster and more accurate. The system can automatically adjust shipments in real time by linking SKU-level inventory data with transportation schedules based on stock availability and order requirements.
Integrated data benefits transportation management. The LMS can track shipment progress, identify bottlenecks, and suggest alternate routes, minimizing delays and reducing fuel consumption. With end-to-end visibility and integrated tools, companies can better sync inventory and shipments, reducing the risk of overstocks or stockouts and lowering transportation costs.
Benefits of a Unified LMS
Centralizing and automating logistics processes leads to faster operations and minimizes disruptions. With a unified LMS, teams can quickly identify bottlenecks, proactively address issues, and optimize resources. This reduces downtime, speeds up deliveries, and improves service levels.
Lower Operational Costs
A unified LMS optimizes resources and improves planning by reducing errors and lowering operating costs. With automated workflows, consolidated data, and the elimination of redundant systems, companies can cut down on overhead and avoid unnecessary delays.
Better Decision-Making with Real-Time Data
One of the greatest advantages of a unified LMS is access to real-time data. With accurate, up-to-date information at their fingertips, managers can make faster, smarter decisions. From adjusting routes to reallocating inventory, real-time data delivers the insights needed to keep operations running smoothly and efficiently.
Improved Customer Satisfaction
With a unified LMS, companies can ensure they’re providing timely, reliable deliveries. Streamlined operations allow them to consistently meet deadlines and reduce transit times, raising CSAT scores. Companies can increase loyalty and sales through improved order fulfillment accuracy and reduced delays.
Overcoming Implementation Challenges
Integrating a unified LMS into an existing logistics environment can present challenges, particularly for companies overly reliant on embedded legacy systems. Connecting the LMS with a transportation management system (TMS), warehouse management system (WMS), enterprise resource planning (ERP), etc., requires careful planning and execution. A staged approach helps ease the transition, allowing teams to adapt while minimizing downtime and service disruptions.
Training and Change Management
The transition requires thorough training and change management so teams become comfortable with the new system. Effective training helps them understand how to use it efficiently, while change management eases the cultural transition to a data-driven approach.
Data Security and Compliance
As logistics increasingly goes digital, data security and regulatory compliance are huge priorities. For instance, a unified LMS helps companies doing business in Europe meet major data privacy regulations such as GDPR. Ensuring that all systems are secure and up to date helps protect sensitive customer and financial data while maintaining trust.
The Impact on Long-Term Business Growth
A unified LMS can scale and adapt to changes in demand, making it a key asset for companies during rapid market changes. As they expand into new markets or roll out product launches, it gives them the flexibility to meet new demands without compromising performance.
Fostering Innovation
A unified LMS reduces complexity, freeing up resources that can be reinvested into innovation. Companies can now pursue emerging technologies like AI-driven analytics, predictive forecasting, and automation, improving supply chain efficiency and creating a competitive advantage.
Competitive Advantage
A simplified, efficient logistics operation makes companies more nimble and responsive to market changes. Optimizing routes, reducing transit times, and improving inventory management all lead to better business outcomes and future positioning.
Playing the Long Game Through Unified Logistics
A unified LMS is essential for reducing operational complexity and increasing supply chain efficiency. By integrating key logistics functions into a single platform, companies can improve communication, streamline workflows, and make smarter, data-driven decisions. This helps foster cost savings, boost customer satisfaction, and improve competitiveness. It also allows them to keep pace with evolving demands in logistics and supply chains while ensuring greater resilience and scalability.
Tramm, an innovative supply chain software firm, has created the first SaaS platform that allows companies to easily manage all owned and third-party transportation assets. Tramm is purpose-built to streamline supply chain operations, acting as a unified LMS by synching data and creating a single source of truth. By eliminating silos and tapping the power of AI-driven insights, Tramm ensures consistency of action across the supply chain.
With its modular, scalable architecture, Tramm’s solution set includes an order management system (OMS), a visibility and control tower module, a global transporter module, a dashboards module, and a driver app. Its platform marries flexibility with optimization, powering a customer-centric approach that delivers measurable results. To learn more about Tramm’s ability to power synchronized logistics and increase supply chain efficiency, request a demo today.
Related Resources
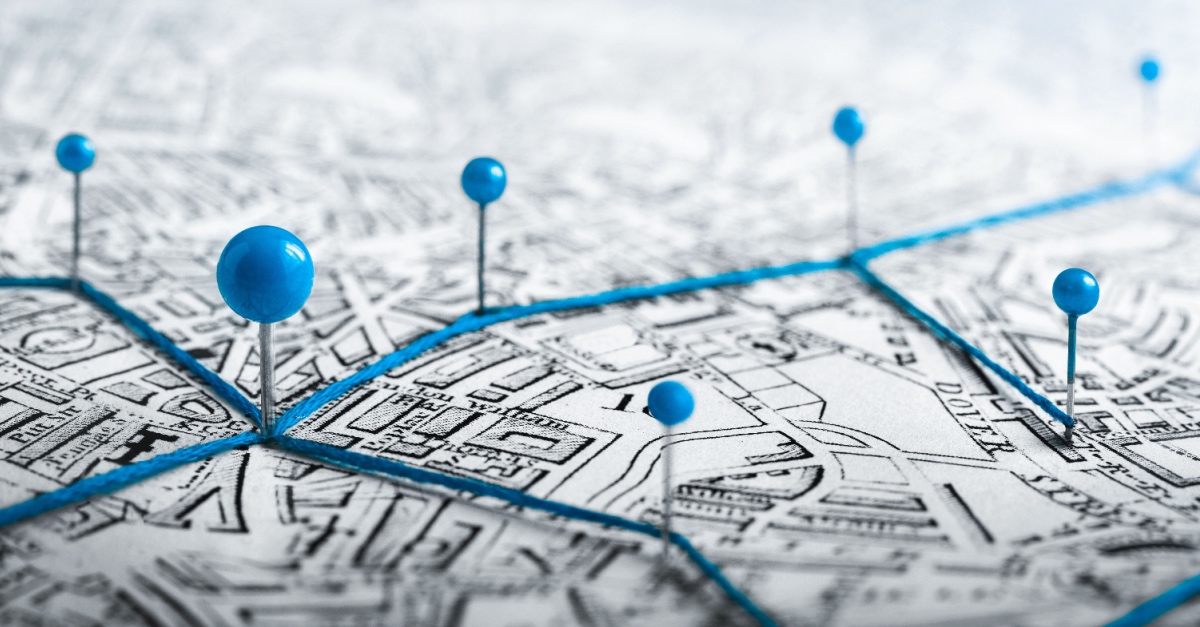
Route Optimization: The Key to Effective Logistics Planning
Listen to any quarterly earnings call from major logistics services firms like UPS and FedEx, and you’re bound to hear a plethora of statistics that deal with delivery performance: average miles per delivery stop, stops per route, packages per driver hour, cost per package, on-time delivery rate, etc.
These figures matter a great deal because they help determine the company’s profitability (or loss) that quarter, as indicators of operating performance expressed in KPIs. They also have a great deal to do with the concept of route optimization, the art and science of executing deliveries as efficiently as possible.
Within the broader scope of logistics planning – coordinating the movement, storage, and flow of goods within a supply chain – route optimization plays a key role. Transportation managers put a great deal of effort into reducing total miles, eliminating delays, and improving route density metrics (number of stops, packages per stop, per driver, etc.). Performance goals include higher on-time rates, lower operating costs, and higher customer satisfaction, among other key business objectives.
We’ll take a closer look at route optimization, why it matters, how it’s achieved, and the technology behind it.
Aspects of Route Optimization
In logistics and transportation, whether truckloads from a plant to a distribution center or stepvans from a hub to a local run, route optimization involves finding the most efficient travel paths. Factors include the distance between points, traffic patterns, delivery windows, fuel costs, and vehicle capacity.
Determining the best fleet to use in each case is also an important success factor. Transportation managers must not only select between different vehicle types and sizes for each set of deliveries, but also the right number of each type based on fixed and variable costs. Fixed costs include driver salaries and wages, vehicle leasing or depreciation, insurance, licensing and permits, and administrative costs. Variable costs include fuel, driver overtime, maintenance and repairs, tolls, loading and unloading, and third-party fees when using a logistics provider.
In addition to vehicle type and size, other route optimization variables include product suitability and restrictions (i.e., refrigerated), road networks, customer time windows, backhaul opportunities, driver hours of service (HOS), efficient load building, and fuel/rest stop planning.
Balancing fixed and variable costs is important because it helps achieve route optimization by minimizing the total cost per delivery while maintaining efficiency and delivery schedules. By selecting the right number of vehicles, adjusting for stop density, and optimizing distances, businesses can achieve substantial savings and performance gains.
Why Route Optimization is Crucial
Through route optimization businesses can achieve greater cost efficiency, improve delivery performance, and foster sustainability. By identifying the most efficient travel routes, they can minimize fuel consumption, lower labor costs, and reduce vehicle wear and tear. This is particularly important in a competitive environment where even small cost savings can spell the difference between a division’s profit and loss.
Optimized routing helps ensure timely deliveries, improving service reliability and customer satisfaction. From an environmental perspective, it means reduced fuel usage and lower carbon emissions, supporting sustainability initiatives and regulatory compliance. This is also something that can resonate with customers who value greener transportation.
Route optimization also helps companies maximize resource utilization through increased efficiency of vehicle, driver, and asset usage. By balancing fleet capacity, stop density, and delivery schedules, transportation managers can reduce empty miles and truck idling. The result: more streamlined operations, better use of resources, and improved performance.
Logistics Challenges Affecting Route Optimization
It’s hard to believe given technological advances across logistics functions, but manual route planning is still widespread, especially among small to mid-sized businesses. Many companies continue to rely on a combination of spreadsheets, paper maps, or simple routing tools for delivery and route planning. These methods are often in use when delivery volume is manageable and the network is relatively small. But they are inefficient, lack scalability, increase costs and risk customer dissatisfaction.
As supply chains become more complex and expectations increase, the use of route optimization software is growing. Advanced tools like transportation management systems (TMS), GPS tools, and AI are becoming much more common. They all leverage real-time data, machine learning and predictive analytics to optimize routes based on factors such as traffic, weather, fuel costs, and delivery windows.
Larger enterprises – both logistics providers and shippers – rely heavily on advanced route optimization technology to manage vast delivery networks. As e-commerce growth and customer expectations rise, more companies are shifting toward automated solutions to stay competitive and improve operational efficiency.
The Role of Technology
Technology has revolutionized route optimization, enabling businesses to streamline logistics and reduce costs. Route optimization software integrates GPS, telematics, and algorithms, analyzing real-time and historical data to create the most efficient travel paths. These tools consider variables like traffic patterns, weather, delivery time windows, and vehicle capacity.
AI and machine learning enhance these capabilities with predictive analytics, looking at traffic trends, fuel costs, and customer demand to anticipate delays and proactively recommend adjustments. Machine learning models continuously refine routing strategies by analyzing historical data, improving accuracy and adaptability.
By integrating these technologies into logistics planning, companies can reduce total miles driven, minimize delays, and optimize resource use. This helps them achieve their key goals (cost savings, higher on-time delivery rates, improved customer satisfaction).
Key Features of Route Optimization Software
Route optimization software gives logistics managers an advanced tool for improving efficiency and reducing costs. A key feature is vehicle selection. When the optimal vehicle is chosen for each route based on capacity, cost, and suitability, it maximizes utilization and reduces costs. Dynamic route adjustments allow for real-time updates based on changing traffic, weather conditions, or unexpected delays, helping maintain on-time performance.
Multi-stop optimization efficiently sequences stops for deliveries, reducing total miles driven and improving route density. Beyond basic stop sequencing, route optimization software should be designed to handle the complexity, nuances and business rules of each company. This could include factoring things like load building based on relative item weight, customer delivery windows, and site restrictions, to optimize stop sequencing.
System integration ensures seamless communication with WMS, TMS, and fleet management systems (FMS), providing end-to-end visibility across functional areas. And driver behavior analytics enhance efficiency and safety by monitoring factors such as speed, braking patterns, and fuel consumption.
Best Practices for Implementation
Successfully implementing route optimization software requires a strategic approach. Start by defining clear objectives that align with your business goals. This includes identifying key metrics such as cost savings, delivery speed, or carbon emissions reduction in order to measure success effectively.
Invest in scalable technology that can grow with your business. As you expand or deal with demand spikes, the solution should be able to adapt to meet changing demands without disrupting workflows.
Provide thorough training in order to maximize the benefits of routing tools. A well-trained workforce leads to better decision-making and greater efficiency.
Prioritize continuous monitoring and adjustment. Real-time analytics can identify inefficiencies, respond to changing conditions, and fine-tune processes. Regular reviews ensure the system continues to deliver value over time and adapts to evolving challenges.
Partnering with the Right Technology Provider
Key characteristics to look for include proven expertise in logistics software and analytics, as well as an understanding of your industry's specific needs. Scalability is another important requirement, future-proofing the technology so it can grow with your business and adapt to changing needs. The ability to provide seamless integration via API or EDI with WMS, TMS, and FMS sets up real-time data sharing and better collaboration across the supply chain.
The right provider should be able to deliver a realistic implementation timeline that factors in data readiness, integration complexity, user training and any customization. For SMBs with fewer requirements, it can happen in a matter of weeks; in more complex enterprise scenarios it can take 3-6 months, often in a phased rollout.
Continuous updates ensure the technology stays on track with advances in AI, machine learning, and predictive analytics. The provider should also be able to deliver a tailored solution that addresses your unique requirements. This will help optimize performance, increase efficiency and cost savings, and improve delivery speed and accuracy, delighting customers and building loyalty.
A Tech-Driven Route To Greater Transport Efficiency
Route optimization has become a cornerstone of supply chain management, and a reliance on outdated manual processes falls woefully short of achieving its goals. Through advanced technology, businesses can become more efficient, save on costs, and improve customer satisfaction and sustainability.
Tramm, an innovator in supply chain technology, has developed a cloud-based end-to-end TMS platform that combines route planning and load building, transporter management, order management, a logistics control tower, and a mobile app. With this approach, Tramm has solved the problem of fragmented supply chain systems, integrating key functions into a unified, scalable system.
Tramm’s Planning and Optimization Module leverages powerful algorithms to handle complex routing environments, accounting for variables that accurately reflect on-the-ground transport operations. Its dynamic multi-day route planning handles scheduling for primary, secondary, and service-based fleets. Users can easily make real-time adjustments based on changing needs, including “what if” visualization and scenarios. A load builder/stackability app automatically plans loads that are tightly synced with capacity and route optimization.
To find out how Tramm’s unified approach can drive transportation efficiency and cost savings while helping you realize sustainability goals, request a demo today.
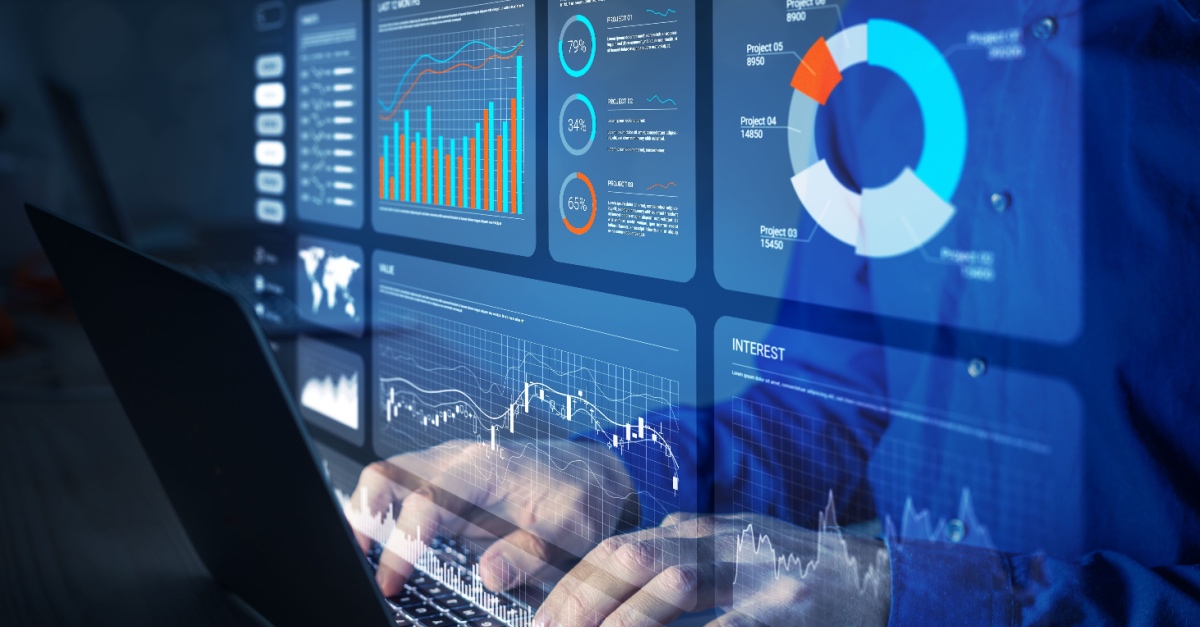
Supply Chain Analytics for Supply Chain Management: Three Tactics To Improve Efficiency
Supply chain analytics is the process of studying historical, transactional, and real-time data in order to uncover ways to improve supply chain efficiency and performance. As such, it is a vital function of any organization involved in the transportation of goods, addressing not only cost management but performance management.
And supply chain management has grown more complex, with frequent disruptive factors the norm, on top of major pandemic shocks that exposed flaws needing strategic resets. In this context, supply chain analytics are called upon more than ever to surface patterns and insights that drive intelligent decisions.
This article will present three key tactics for effectively implementing supply chain analytics, helping companies drive down costs and improve performance.
Modern Supply Chain Management Demands Modern Supply Chain Analytics
To define it further, supply chain analytics pulls in data from throughout the supply chain (procurement, manufacturing, inventory, orders, and distribution) for deep analysis in order to predict and improve performance. This data comes from external (carriers, partners, suppliers) as well as internal (ERP, SCM, TMS, WMS, inventory management, OMS, etc.) sources.
The ability to gain supply chain efficiency by improving data analytics can achieve a number of important business goals. This includes (but is not limited to):
- Minimizing inventory carrying costs
- Optimizing order fulfillment
- Proactively managing material costs
- Avoiding stockouts and overstocks
- Managing suppliers and purchases
Supply chain analytics also empowers businesses to engage in data-driven decision-making in the supply chain that can lower costs and improve resiliency and responsiveness. They can anticipate challenges and adapt to market fluctuations, helping them maintain a competitive edge even as challenges proliferate.
Three Tactics for Effective Implementation of Supply Chain Analytics
In order to receive the full benefit of supply chain analytics, companies need to look at it strategically and implement tactics designed to drive results in supply chain management. Here are three ways to achieve this.
Tactic 1: Integrate Data Across the Entire Supply Chain
The ability to gain a unified view of data across the supply chain is foundational in making supply chain analytics work effectively and glean actionable insights. This requires data feeds, ideally through API integrations, from all internal and external sources.
It’s often easier said than done. Data silos and fragmented systems, unfortunately, are still a thing. Enterprise systems that can’t communicate without IT intervention pose a challenge to integration.
One surefire way to achieve effective data integration is by using a true supply chain TMS that centralizes data from across multiple sources, such as those listed above (orders, shipments, inventory, etc.). A key prerequisite is compatibility with your current tech stack (ERP, WMS, TMS, etc.).
Tramm is a comprehensive TMS that is purpose-built to streamline supply chain operations within a unified platform approach. Its integration capabilities unify data from across the supply chain, creating a single source of truth. Tramm’s consolidated platform helps teams pull together actionable insights based on real-time data. This unified approach eliminates data silos, streamlines processes, and ensures consistency of actions across the supply chain.
Tactic 2: Implement Real-Time Analytics for Proactive Decision-Making
Real-time analytics is the process of analyzing and responding to data as it's generated, with the goal of providing quick insights to help users make better-informed decisions. Conversely, relying on delayed or outdated data acts as a drag on supply chain performance.
It's often used in applications where the timeliness of data is critical, such as in supply chain and logistics. Artificial intelligence and its cousin, machine learning, have added the ability to quickly read, comprehend, and correlate data from across sources, advancing real-time analytical capabilities.
Adopting a TMS with real-time data processing and monitoring capabilities ensures a seamless data flow and communication between systems and stakeholders. For example, Tramm’s FleetVision control tower module provides real-time vehicle tracking through integration with telematics, and status updates. It enables communication with all stakeholders via WhatsApp, SMS, or email for visibility into delivery status, deviations, and reporting.
Tactic 3: Utilize Advanced Analytics for Predictive and Prescriptive Insights
In the context of supply chain management, predictive analytics takes historical, transactional, and real-time data to create models that identify patterns for risks and opportunities. This helps guide decision-making by anticipating specific future events.
Prescriptive analytics takes this process a step further. It pulls together insights gleaned from predictive data analysis to suggest optimal actions, anticipating and solving potential issues before they arise.
This type of advanced capability for supply chain management involves integrating AI and machine learning to drive both predictive and prescriptive analytics. Staff must be adequately trained and processes aligned to take full advantage of these tools for real-time decision-making that drives greater supply chain efficiency.
Tramm’s advanced analytics include both predictive and prescriptive tools that optimize routing, and risk management. Tramm enables businesses to anticipate future challenges and take proactive steps in response. This type of real-time decision-making improves supply chain efficiency and resiliency.
Analytics Power Better Supply Chain Management
In reality, supply chain analytics is what drives supply chain management. The ability to pull in and quickly analyze internal and external data to formulate strategies and inform decisions is a foundational discipline. Mix in a complex global economy and disruptive events, and this capability becomes even more critical.
Tramm gets this, which is why it has developed a comprehensive suite that helps companies address multiple aspects of supply chain management. Its innovative supply chain TMS provides in-depth performance analytics backed by real-time data. Users gain planning and route optimization (Planning and Optimization Module), transporter management (Transact Module), real-time visibility (FleetVision Module) and impactful business insights (Dashboard Module), and much more. To learn more about how Tramm can transform your supply chain management, request a demo today.
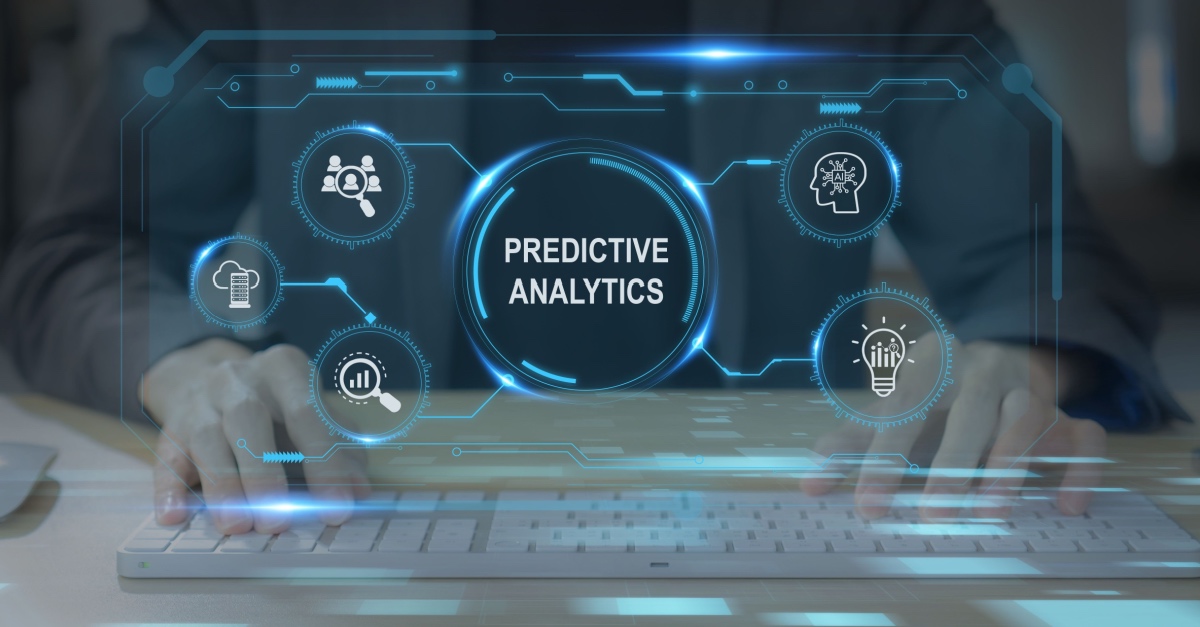
Predictive Analytics in Logistics: The Key to Effective Supply Chain Management
It’s hard to say “supply chain” without throwing in the word “complexity” as a qualifier. Supply chain management has grown more challenging for a number of reasons. Many businesses, both B2B and B2C, have become “omnichannel,” mixing online and offline, while geopolitical strains have disrupted shipping. The pandemic effect led to widespread supply chain redesign and rethinking, including diversifying sourcing, carriers, ports and lanes, etc., to guard against future shocks.
Predictive analytics has become a key capability across industries and business functions. Smart digital tools are used to analyze vast amounts of data, helping companies gain insights and plot strategies with a more forward-looking bent. In logistics and supply chain, predictive analytics has become an invaluable tool, leveraging historical and real-time data to more effectively set transportation, logistics, and warehousing strategies.
We will explore how predictive analytics is transforming supply chain management. It has become essential for everything from demand forecasting to shipping schedules and route optimization.
Supply Chain Analytics: Insights Made Actionable
Predictive analytics applies advanced algorithms and statistical models to identify patterns, trends, and correlations within the data to generate forecasts about future events or behaviors.
In the context of supply chain management, predictive analytics takes historical and transactional data to create models that identify patterns for risks and opportunities. This helps guide decision-making by anticipating specific future events.
For instance, predictive analytics can be used to help a company shift from a just-in-case to a just-in-time model for sourcing products and materials, or use analysis of next quarter’s freight rates to optimize carrier selection and contracting.
Effective Supply Chain Management Begins with Effective Analytics
The proactive approach enabled by predictive analytics helps businesses optimize key supply chain functions such as inventory management, transportation planning, and demand forecasting. It does this by making resource allocation more efficient while minimizing the impact of disruptions.
Common techniques in predictive analytics for supply chain management include regression analysis, time series forecasting, decision trees, and neural networks. Each has its unique strengths and application to specific areas, such as route planning and risk mitigation.
Ensuring compatibility between predictive analytics tools and existing IT infrastructure can be challenging. Balancing innovation with operational continuity is key to leveraging predictive insights effectively. And breaking down silos to enable seamless data flow across systems is critical but often difficult to achieve. This is why a smart option is to go with an end-to-end supply chain management platform approach, using an integrated suite of tools that comes pre-built with powerful analytics capabilities.
Three Ways Predictive Analytics Can Revolutionize Supply Chain Management
Let’s dive a little deeper into specific areas of supply chain management where predictive analytics can drive operational efficiency.
Enhancing Demand Forecasting and Inventory Management
Predictive analytics significantly enhances demand forecasting accuracy, enabling businesses to better align inventory levels with future demand. By analyzing historical sales data, market trends, and external factors, predictive models provide insights into upcoming demand patterns.
This leads to more precise inventory planning, reducing the risk of overstock and stockouts. Benefits include cost savings from reduced holding costs and waste, along with improved customer satisfaction due to consistent product availability.
Optimizing Transportation and Route Planning
Predictive analytics also plays a crucial role in optimizing transportation and route planning. By anticipating potential delays, disruptions, and inefficiencies (traffic congestion, weather conditions, etc.), predictive modeling drives more efficient route planning. This reduces transit times, lowers fuel costs, and minimizes carbon emissions, saving money while taking a more sustainable approach.
Tramm, the creator of a true supply chain TMS, has a Route Optimization Module that utilizes predictive analytics to adjust routes in real time based on a variety of factors, ensuring timely deliveries while maximizing efficiency. It also helps companies optimize cross-dock and multi-modal planning, including LTL, TL, and multi-fleet.
Proactive Risk Management and Issue Resolution
By identifying potential risks (supplier delays, transportation bottlenecks, port disruptions) before they materialize, businesses can get ahead of these risk factors. Early warning systems and scenario planning, powered by predictive analytics, help maintain supply chain resilience and continuity.
Tramm’s Control Tower Module uses the power of predictive analytics to monitor and manage potential disruptions. A dashboard view provides real-time vehicle tracking and status updates via third-party integration, GPS, or Tramm’s Mobile App. Customizable alerts notify managers about unplanned stops, deviations, and performance issues, minimizing the impact of unforeseen events.
Tapping the Power of Predictive Analytics for Supply Chain Optimization
Predictive analytics is transforming supply chain management by allowing companies to optimize demand forecasting and transportation, and proactively manage risk. These capabilities allow them to make data-driven decisions, improving efficiency and supply chain resilience. The efficiencies gained help reduce costs and improve competitiveness.
Tramm’s platform is built on a simple yet rarely implemented idea: a TMS can only be effective if every aspect of transportation management is modeled, integrated, and visible from order inception to final delivery. The power of Tramm comes from its ability to capture and leverage details in a user-friendly way. Users gain planning and route optimization, transporter management (Transact Module), real-time visibility (FleetVision Module), and impactful business insights (Dashboard Module). To learn more about how Tramm can transform your supply chain management, request a demo today.
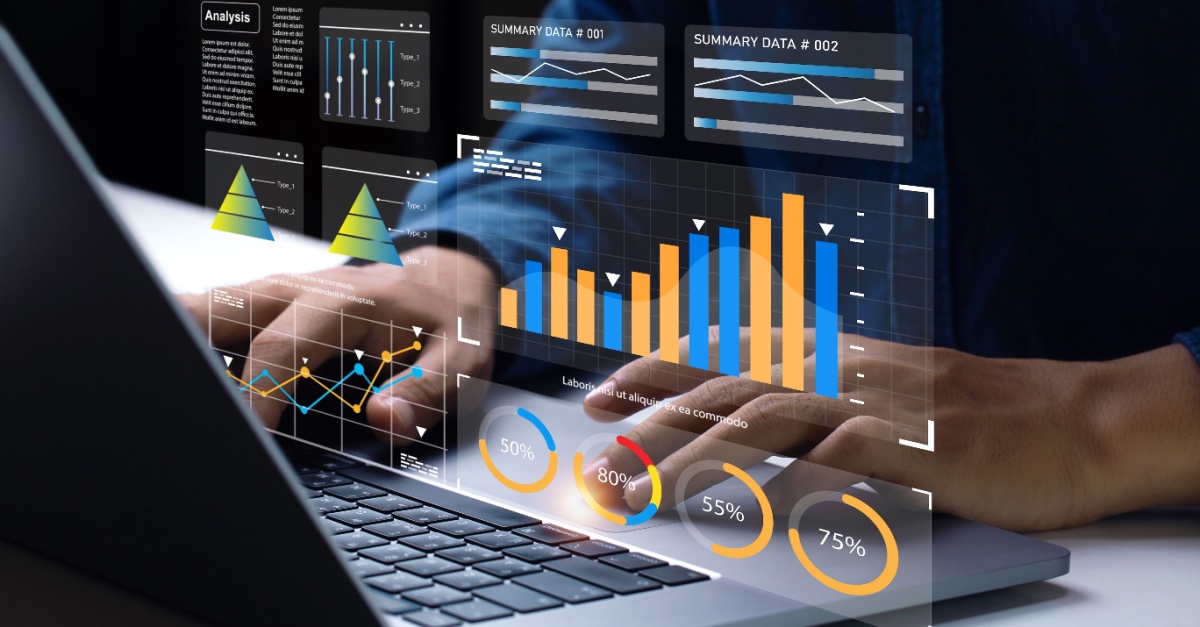
The Importance of Detailed Order Data in Supply Chain Optimization
As supply chains become increasingly complex, the demand for efficiency and flexibility has never been greater as companies struggle to meet rising customer expectations and deal with global disruptions. Having detailed order data is one key ingredient in supply chain optimization, enabling better decision-making, improved efficiency, and reduced costs.
The ability to access and analyze clean, accurate data improves demand forecasting, inventory management, and fulfillment operations by providing greater visibility into SKU levels and order status. It also helps streamline transportation, reduce lead times, and optimize carrier selection.
Conversely, a lack of detailed order data leads to a variety of negative consequences. These include mismanaged inventory (more stockouts, overstocks), fulfillment delays, disrupted workflows, inaccurate demand forecasts (over or underproduction), strained customer relationships, and financial impacts.
This is why order data accuracy is critical in supply chain optimization. It improves decision-making, enhances efficiency, and reduces costs.
Understanding Order Data’s Role in Supply Chain Optimization
Order data includes information on products, quantities, prices, customer preferences, delivery schedules, and fulfillment status. Sources of order data include order management systems (OMS), enterprise resource planning (ERP, often the central hub), customer relationship management (CRM), procurement systems, and, if there’s a retail component, point-of-sale (POS) systems.
Detailed order data is the foundation for optimizing inventory management, transportation and delivery, warehousing, and fulfillment — in short, every operational aspect of the business.
An inability to control how orders are handled from inception contributes to poor decisions, and inaccurate data is often the culprit. The lack of a unified, efficient system for moving orders from planning to execution and doesn’t enable real-time visibility is a recipe for disaster. The result is a limited ability to represent actual order status in a meaningful way.
Enhancing Demand Forecasting and Inventory Management
A business’s success or failure is inextricably linked to its ability to accurately forecast demand and, from there, properly manage inventory levels. Detailed order data (current and historical), as well as factors like market trends and customer feedback, allow businesses to predict demand more accurately and optimize inventory levels.
Using manual processes to handle order data, even in small-to-medium businesses, is a system rife with errors and inaccuracies. The ability to access real-time order data informs smarter reordering and replenishment strategies. This helps reduce overstocks or out-of-stocks by leveraging actual demand patterns, maintaining cash flow, reducing carrying costs, and keeping customers happy.
Improving Order Fulfillment and Reducing Lead Times
Having detailed order data helps minimize fulfillment errors by optimizing picking, packing, and shipping processes. By accurately tracking customer demand, businesses can expedite order processing and optimize transportation routes to reduce lead times.
Order allocation can be fine-tuned based on stock availability and proximity to customers, enabling faster, more efficient fulfillment. This not only speeds up deliveries but also improves customer satisfaction.
Optimizing Transportation and Logistics
Another benefit of having detailed, accurate order data is on the logistics side. With it, businesses can optimize order routing, consolidate shipments, and reduce delivery costs. They can also choose the most cost-effective carriers and shipping methods based on order data.
Order consolidation involves centralizing items from multiple orders into a single location or by combining multiple orders from different sales channels into a single system. This helps lower transportation costs, improve inventory management, simplify logistics, and provide a better customer experience by reducing split shipments.
With the ability to access and analyze detailed order data, businesses can save by taking advantage of bulk shipping discounts, optimizing carrier selection, and avoiding last-minute changes in shipping schedules.
Supporting Customer Satisfaction and Personalization
Detailed order data allows businesses to track customer preferences, providing personalized offerings and recommendations. It also improves proactive communication, informing customers about order status, estimated delivery times, and potential delays.
This type of transparency enhances trust and helps companies to manage customer expectations. It contributes to a consistently excellent customer experience, boosting satisfaction scores, repeat business, and brand loyalty.
Without Detailed Order Data, Things Break Down
Detailed order data is critical for supply chain optimization, enabling better demand forecasting, more efficient inventory management, and faster fulfillment. It allows businesses to streamline transportation, optimize routing, and reduce delivery costs. Accurate order data also supports customer satisfaction by providing real-time order status and personalized offerings, reducing errors and improving efficiency. A lack of such data, for instance, due to manual processes or outdated software, leads to fulfillment delays, inventory mismanagement, and strained operations.
Tramm, a developer of a leading unified supply chain management platform, combines a powerful OMS within its transportation management system (TMS) suite. This integrated approach provides end-to-end visibility and control over order fulfillment and shipping processes. Tramm’s Order Management Module ensures that orders are fully consolidated before being released for shipment, while the TMS manages transportation in the most efficient, cost-effective manner.
The power of Tramm lies in its ability to optimize the entire process from order management through planning and route optimization, contract management, fleet management, and performance analytics. A versatile driver app provides workflow management, electronic proof of delivery, compliance tracking, and auditing.
Request a demo today to learn more about how Tramm can drive supply chain optimization through its cutting-edge tools and holistic approach.
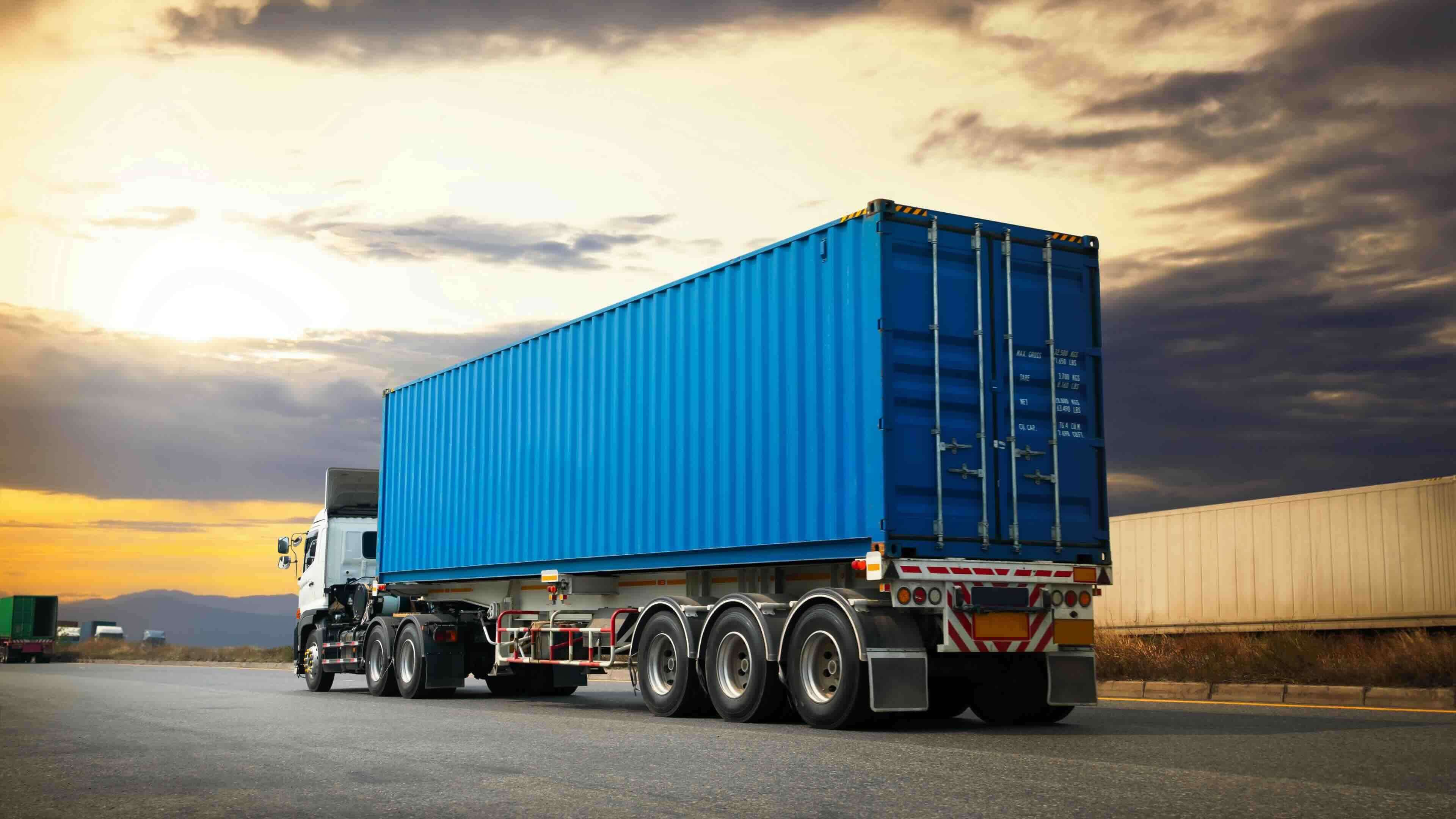