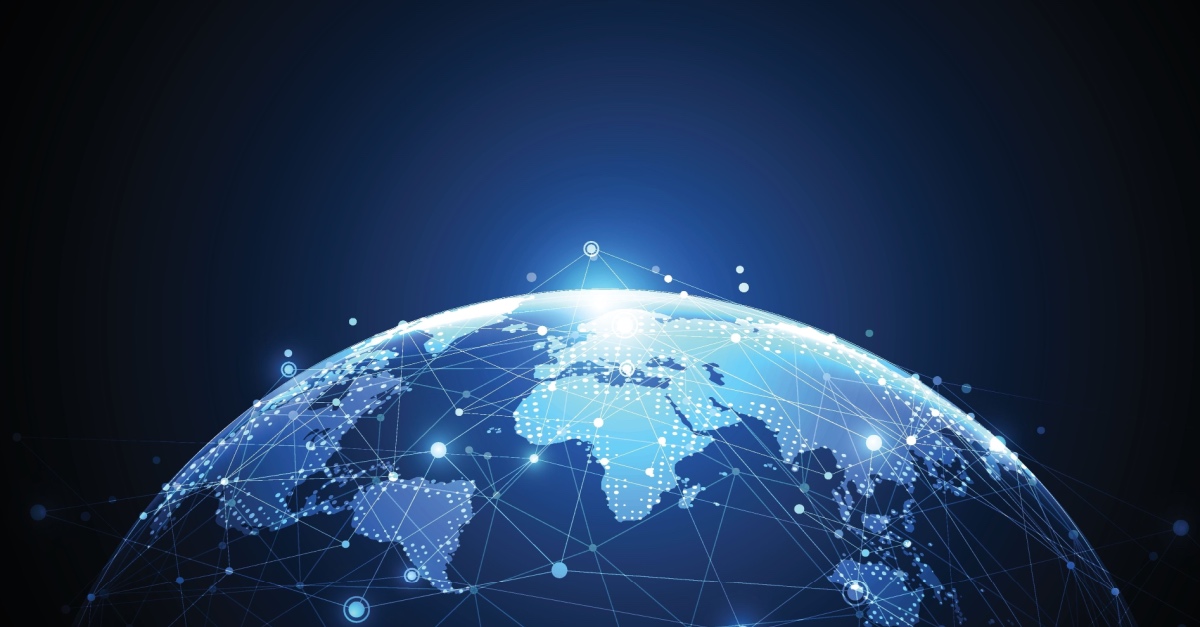
Today’s highly interconnected supply chains are, in effect, massive networks that rely on all the players to do their part. Despite this, inadequate communication often results in lackluster coordination and is a primary chokepoint, leading to any number of failures. That’s why implementing a true supply chain TMS (transportation management system) is a key success factor.
TMS software is one way organizations look to create unified communication among supply chain stakeholders. Unfortunately, most systems today fail to achieve this objective, as they’re cumbersome, inflexible, and out of sync with interdependent pieces of the tech stack.
A lack of integrated communication and collaboration among external and internal supply chain partners ultimately frustrates customers and leads them to jump ship. Throw in all-too-common disruptions — tight capacity, port backups, geopolitical conflicts — and companies with poor supply chain visibility can’t give customers the kind of transparency they’ve come to expect.
This is where Tramm comes in. Tramm is a comprehensive TMS that is purpose-built to streamline supply chain operations within a unified platform approach. By integrating communication, route optimization, order management, and a control tower for real-time visibility, Tramm ups efficiency, reduces costs, and helps improve CSAT scores. All of this addresses critical pain points felt today across logistics management.
In this article, we’ll explore the issues and limitations of TMS systems and how Tramm addresses them by enhancing communication across the supply chain. We’ll unpack how Tramm is built on a simple yet rarely implemented idea: a TMS can only be effective if every aspect of transport management is modeled, integrated, and visible from order inception to final delivery.
Communication: A Key Chokepoint for Complex Supply Chains
In logistics, every operational execution — whether store delivery, inbound DC shipment, or DTC order — touches multiple functional areas: transportation, order management, customer data, and warehouse management. Without a unified communication approach, things can break down quickly, as we’ll illustrate with this hypothetical scenario:
Jessica orders a dress for a friend’s wedding that's four days away, choosing the retailer’s two-day delivery. The OMS confirms her purchase, but an inventory system error shows it as in stock at a nearby store for e-commerce fulfillment when, in reality, it’s sold out. The next day, the same dress is located at a warehouse 500 miles away, and the order is re-routed, adding a day in transit.
Three days after the order was placed, it’s out for delivery, but the truck breaks down on the way. Due to poor fleet visibility, a delivery status update isn’t communicated to Jessica. On top of that, an address change she entered on the e-commerce website goes into the CRM, but this data isn’t synced with the TMS. So, a driver leaves the package at her old address. Jessica, anxiously trying to track her order, contacts customer service, but a lack of synchronization between systems leaves her without answers. The dress finally arrives — a day after the wedding — and a high-value customer is lost.
This unhappy ending demonstrates how vital seamless communication is, given the intricate nature of today's supply chains, where even a minor failure has financial repercussions. Think, for example, of the high cost of customer acquisition vs. retention.
We’ll now look at three specific challenges of supply chain communication faced by organizations today.
Fragmented Systems
Fragmented systems create significant barriers to effective communication. This disconnection leads to the creation of information silos across disparate systems, making it hard for each operations team to access accurate, consistent data. Poor integration hampers their ability to coordinate assets and tasks, increases the likelihood of errors, and reduces operational efficiency.
Inconsistent Data
Inconsistent data poses a major supply chain challenge, as variations in formats and sources lead to bad information and worse decisions. This undermines the reliability of communication, causing confusion and errors. Ultimately, it hampers your ability to coordinate effectively with other functional teams, limiting efficiency and dinging customer satisfaction.
Manual Processes
Manual processes increase the risk of errors and slow down the flow of crucial information. Depending on paper-based methods often causes delays and makes it difficult to maintain accurate, timely communication. This ultimately impacts decision-making and results in poor operational performance.
To quote Strother Martin to Paul Newman as the cruel prison captain in “Cool Hand Luke”: “What we’ve got here is … failure to communicate.” Updates from manual processes, sometimes using Excel sheets, is a recipe for disaster, especially considering the need for real-time data sharing between systems, internal teams, carriers, 3PLs, and customers.
Integrated Communications: Revolutionizing Coordination with Supply Chain TMS
Tramm has developed an innovative TMS solution that integrates supply chain communications in a single powerful, intuitive platform. It ties together order management, route optimization, planning and scheduling, carrier management, a control tower for shipment visibility, and a mobile app with customizable workflows and electronic proof of delivery (ePOD) for driver management.
A true supply chain TMS, Tramm offers broad optimization across many aspects of logistics operations, from order processing to delivery, carrier billing, returns, and exception management. The results are greater efficiency, reduced costs, improved performance (order accuracy, on-time delivery, etc.), and enhanced customer satisfaction.
Tramm’s configurable solution has many automation capabilities for a variety of supply chain functions, including alerts for off-plan events, automated reporting, driver debriefing, and communication via standard tools (WhatsApp, email, SMS) with customers, drivers, and managers.
Here are more details on different aspects of Tramm TMS and what sets it apart from traditional solutions.
Platform Unification
Tramm TMS addresses the problem of fragmented supply chain systems by integrating key functions into a unified, scalable platform. It centralizes data, ensuring consistency, accuracy, and integrated communication. The FleetVision control tower provides real-time visibility into vehicle location and ETAs, route adherence, and load status.
Transportation managers can set up customized, automated workflows to manage drivers and routes via the Tramm mobile app. For instance, it can include detailed instructions such as the level of signature required for each stop, when to scan a code, if a confirmation picture is required, etc.
Information from the app is fed back into the Tramm system for planning, reporting, and performance management purposes. For instance, location data from the driver’s device is compared to the onboard GPS to identify any errors or inconsistencies.
Seamless Data Integration
Tramm TMS centralizes all supply chain data in an accessible, intuitive platform with mobile access. This ensures data consistency and accuracy, eliminates discrepancies, and provides organizations with a single source of truth. Real-time updates and automated workflows further enhance data reliability, improving decision-making and overall supply chain efficiency.
Data usability and accessibility are some of the main benefits. Team members across supply chain functions get access to precise data and analytical insights for improved performance monitoring, planning, and reporting.
Tramm’s platform brings in data from internal as well as external partners (carriers, brokers, freight forwarders, 3PLs, etc.) via APIs. Drivers, managers, planners, and executives all get a unified view via the app to real-time tracking and status information, hours of service remaining, precise delivery locations and pickup requirements, KPIs, and much more.
Automated Supply Chain Accuracy
Tramm TMS alleviates cumbersome manual processes by automating key workflows to reduce reliance on manual data entry and paper-based methods. It streamlines operations with dynamic updates, integrated communication tools, and centralized data management.
Tramm’s rules-based order processing automates things like order splitting based on operational and resource requirements, as well as designated delivery days and windows for end customers, with the option of manual intervention where necessary. Tramm’s dashboard includes automated reporting, analytics, and business intelligence capabilities. This empowers decision-makers with a clear understanding of operations, performance, and growth opportunities.
Jessica’s Story, Reimagined
Now, let’s return to our earlier example of the fictional Jessica and her ill-fated dress order, with Tramm as the hero of the story.
Jessica orders her dress, and Tramm’s OMS confirms her purchase, pulling directly from the retailer’s inventory management system to confirm it’s in stock. Tramm also selects the optimal carrier and delivery window based on the customer’s location and the retailer’s requirements, handing this information off to the TMS for dispatch.
On the promised date, the driver, using the Tramm mobile app, notes Jessica’s delivery preference (side door). The ePOD function notifies the system of a successful dropoff for performance monitoring and reporting. Jessica, meanwhile, having received regular notifications of the order in transit at every scan, is thrilled with the experience (and the dress). She has a blast at the wedding, and the retailer gets a smiley rating from their happy customer.
Yesterday’s TMS Can’t Handle Today’s Exacting Supply Chain Communication Needs
How is it possible to have an optimized, efficient supply chain when internal and external data is siloed, and stakeholder communication sometimes feels like today’s equivalent of cans and strings? Answer: it’s not possible.
This leads to all kinds of negative downstream effects: missed opportunities, time-consuming manual processes to cover system gaps, inadequate reporting, and business intelligence insights, poor visibility into assets and deliveries, increased costs, and dissatisfied customers.
Tramm’s unified suite enables shippers, 3PLs, carriers, and their partners to accurately communicate the intricacies of day-to-day supply chain operations. Through our powerful app, control tower visibility, customizable dashboard, and precision planning capabilities, companies can increase efficiency and optimize execution. Analytics and reporting, including KPI-based internal and external scoring, lead to smarter decisions and better outcomes for customers and businesses.
To learn more about how Tramm can make a difference by unifying your supply chain communications, request a demo today.
Related Resources
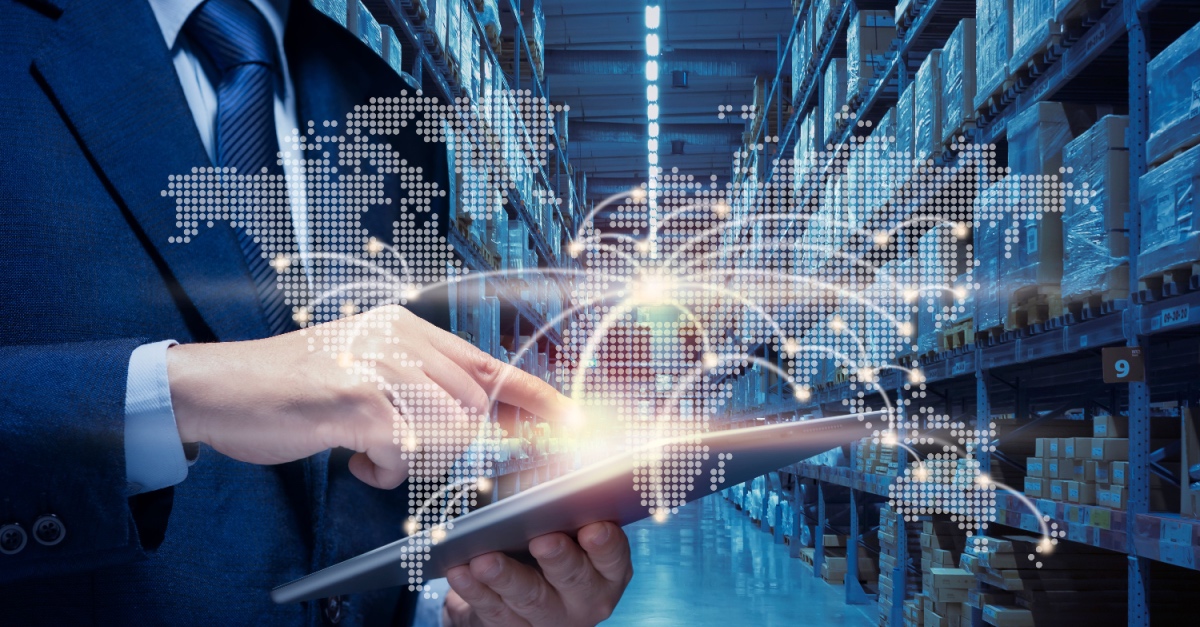
Reducing Operational Complexity With a Unified Logistics Management System
Saying “logistics are complex” may be akin to saying “water is wet,” but the level only seems to be rising. Companies are expanding sales channels, trading partners, vendors, and markets as they seek new opportunities, and each step adds a layer of complexity. In the process, they often pursue a point solution approach, creating a patchwork of technologies that require a heavy IT lift in terms of integration and maintenance.
A logistics management system (LMS, not to be confused with a labor management system) is a technology solution that addresses this issue. It’s a software tool that helps companies manage the flow of goods from production to end customers.
An LMS can help improve efficiency, reduce costs, and provide a better customer experience. It does this by consolidating all logistics operations into one integrated platform. A truly unified LMS can help shippers reduce complexity and improve supply chain resiliency. By coordinating multiple logistics functions within a single system, an LMS eliminates silos and promotes real-time collaboration.
What is a Unified Logistics Management System?
A unified LMS integrates various logistics functions, such as inventory, transportation, and warehouse management. Key features include access to real-time data, automated processes, and end-to-end visibility. By consolidating logistics operations, a unified LMS removes inefficiencies that naturally arise from disparate technologies. The result is improved decision-making and better demand forecasting.
Unification is critical for managing complex, multi-node supply chains under pressure from heightened customer expectations, geopolitical and labor tensions, fluctuating markets, and global sourcing. A unified LMS provides the flexibility and scalability to adapt to new business challenges and opportunities, increasing responsiveness and competitiveness.
The Operational Complexity of Logistics
Managing the flow of goods from origin to customer involves many moving parts. Disparate systems and silos, as noted above, slow down operations and drive inefficiency. This often requires manual intervention to reconcile data across platforms, resulting in errors and delays.
Reliance on manual workflows adds to the operational burden, lowering productivity and increasing the risk of errors. Inventory management, shipping, tracking, and reporting are time-consuming and require coordination across departments, making it difficult to maintain accuracy and efficiency.
The sheer volume of data generated in logistics — customer orders, inventory updates, shipping schedules, etc. — can quickly overwhelm traditional systems. Handling this information load without the proper infrastructure increases complexity and response times, impacting overall supply chain performance.
A Unified LMS: Reducing Operational Complexity
Imagine a centralized platform where all logistics data is stored, providing real-time visibility across operations. This would remove the need to constantly reconcile data across multiple systems. Tracking orders, monitoring shipments, and accessing up-to-date inventory levels would become easier. Real-time data access would also allow logistics managers to make faster, more informed decisions that improve supply chain efficiency.
This type of consolidation reduces errors and eliminates delays caused by manual data entry. Teams no longer need to cross-check information across systems; all stakeholders can access the same accurate data. Greater visibility streamlines coordination among suppliers, warehouse managers, transporters, and customers, leading to faster response times and fewer disruptions.
Streamlining Communication and Collaboration
A unified LMS also enhances internal and external communication by eliminating data silos. This makes it easier to track orders, manage inventory, and resolve issues in real time.
With all logistics operations accessible on a single platform, teams can collaborate more effectively, reduce communication barriers, and increase alignment. This level of coordination improves performance, so every aspect of the logistics process runs smoothly and efficiently.
Workflow Automation
Automating orders, inventory updates, and shipment tracking reduces the need for manual intervention. Automated workflows also help eliminate errors and streamline administrative tasks, freeing up logistics teams to focus on more high-level, strategic activities.
For example, an automated system can trigger the creation of shipping labels, inventory adjustments, and confirmations upon order placement. This ensures that everything is processed rapidly without requiring additional input. Automation helps companies reduce lead times, improve accuracy, and reduce errors in orders and shipping.
Integrated Inventory and Transportation Management
A unified LMS combines inventory and transportation data, optimizing routing while making order fulfillment faster and more accurate. The system can automatically adjust shipments in real time by linking SKU-level inventory data with transportation schedules based on stock availability and order requirements.
Integrated data benefits transportation management. The LMS can track shipment progress, identify bottlenecks, and suggest alternate routes, minimizing delays and reducing fuel consumption. With end-to-end visibility and integrated tools, companies can better sync inventory and shipments, reducing the risk of overstocks or stockouts and lowering transportation costs.
Benefits of a Unified LMS
Centralizing and automating logistics processes leads to faster operations and minimizes disruptions. With a unified LMS, teams can quickly identify bottlenecks, proactively address issues, and optimize resources. This reduces downtime, speeds up deliveries, and improves service levels.
Lower Operational Costs
A unified LMS optimizes resources and improves planning by reducing errors and lowering operating costs. With automated workflows, consolidated data, and the elimination of redundant systems, companies can cut down on overhead and avoid unnecessary delays.
Better Decision-Making with Real-Time Data
One of the greatest advantages of a unified LMS is access to real-time data. With accurate, up-to-date information at their fingertips, managers can make faster, smarter decisions. From adjusting routes to reallocating inventory, real-time data delivers the insights needed to keep operations running smoothly and efficiently.
Improved Customer Satisfaction
With a unified LMS, companies can ensure they’re providing timely, reliable deliveries. Streamlined operations allow them to consistently meet deadlines and reduce transit times, raising CSAT scores. Companies can increase loyalty and sales through improved order fulfillment accuracy and reduced delays.
Overcoming Implementation Challenges
Integrating a unified LMS into an existing logistics environment can present challenges, particularly for companies overly reliant on embedded legacy systems. Connecting the LMS with a transportation management system (TMS), warehouse management system (WMS), enterprise resource planning (ERP), etc., requires careful planning and execution. A staged approach helps ease the transition, allowing teams to adapt while minimizing downtime and service disruptions.
Training and Change Management
The transition requires thorough training and change management so teams become comfortable with the new system. Effective training helps them understand how to use it efficiently, while change management eases the cultural transition to a data-driven approach.
Data Security and Compliance
As logistics increasingly goes digital, data security and regulatory compliance are huge priorities. For instance, a unified LMS helps companies doing business in Europe meet major data privacy regulations such as GDPR. Ensuring that all systems are secure and up to date helps protect sensitive customer and financial data while maintaining trust.
The Impact on Long-Term Business Growth
A unified LMS can scale and adapt to changes in demand, making it a key asset for companies during rapid market changes. As they expand into new markets or roll out product launches, it gives them the flexibility to meet new demands without compromising performance.
Fostering Innovation
A unified LMS reduces complexity, freeing up resources that can be reinvested into innovation. Companies can now pursue emerging technologies like AI-driven analytics, predictive forecasting, and automation, improving supply chain efficiency and creating a competitive advantage.
Competitive Advantage
A simplified, efficient logistics operation makes companies more nimble and responsive to market changes. Optimizing routes, reducing transit times, and improving inventory management all lead to better business outcomes and future positioning.
Playing the Long Game Through Unified Logistics
A unified LMS is essential for reducing operational complexity and increasing supply chain efficiency. By integrating key logistics functions into a single platform, companies can improve communication, streamline workflows, and make smarter, data-driven decisions. This helps foster cost savings, boost customer satisfaction, and improve competitiveness. It also allows them to keep pace with evolving demands in logistics and supply chains while ensuring greater resilience and scalability.
Tramm, an innovative supply chain software firm, has created the first SaaS platform that allows companies to easily manage all owned and third-party transportation assets. Tramm is purpose-built to streamline supply chain operations, acting as a unified LMS by synching data and creating a single source of truth. By eliminating silos and tapping the power of AI-driven insights, Tramm ensures consistency of action across the supply chain.
With its modular, scalable architecture, Tramm’s solution set includes an order management system (OMS), a visibility and control tower module, a global transporter module, a dashboards module, and a driver app. Its platform marries flexibility with optimization, powering a customer-centric approach that delivers measurable results. To learn more about Tramm’s ability to power synchronized logistics and increase supply chain efficiency, request a demo today.
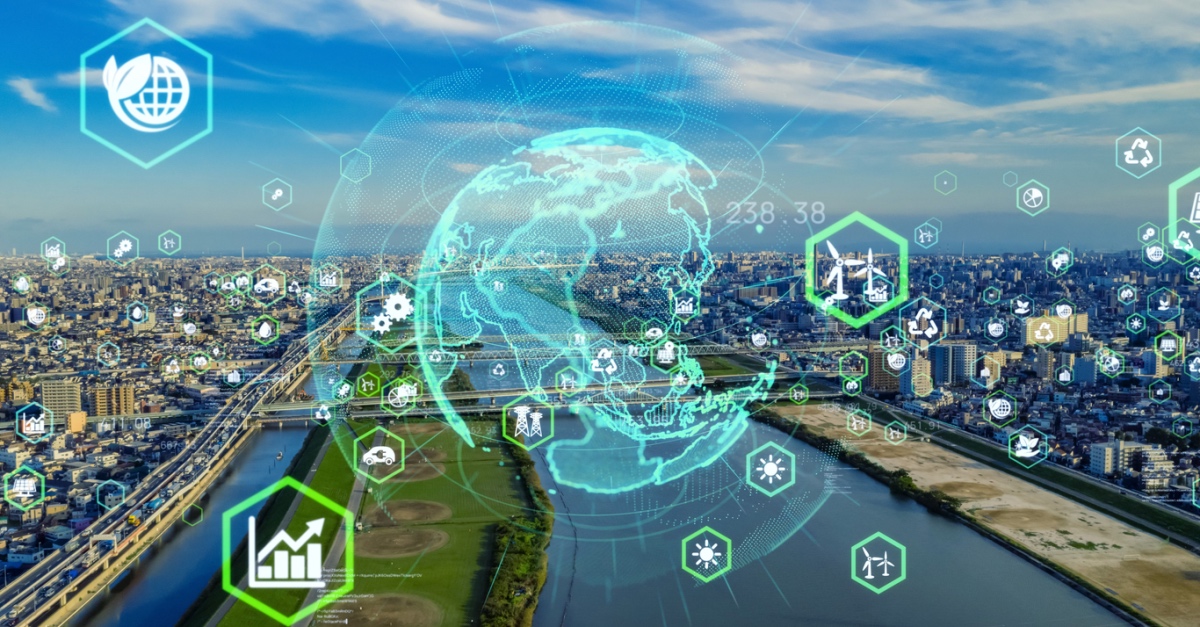
Sustainable Logistics: How Optimized Routing Can Reduce Your Carbon Footprint
The world of logistics and transportation cannot afford to slow down, and the trend toward sustainable logistics is working hard to catch up. Demand for shipping and delivery services is only increasing in a fast-moving, interconnected global economy. But with this growth comes greater pollution levels from vehicles and logistics networks.
For this reason, it shouldn’t be surprising that 75% of logistics companies have a focus on sustainability, according to a May 2024 survey by the Germany-based Logistics Hall of Fame. A majority of respondents rated the risk of financial loss due to climate change as “medium to high.”
This is why major efforts are underway to reduce trucking-generated pollution by implementing a sustainable logistics program. These include efforts to optimize routing, grow alternative fuel fleets, increase the use of automation, enforce stricter emissions standards, and ramp up intermodal transportation.
Optimized routing, in particular, has emerged as a powerful tool to not only reduce transportation costs but also significantly minimize carbon emissions, making logistics operations more sustainable.
The Environmental Impact of Logistics
Transportation contributes more than a third of all CO2 emissions globally, with nearly two-thirds of that coming from trucking, according to the International Energy Agency (IEA). In addition, transportation relies on petroleum products for nearly 91% of its energy, down just 3.5 percentage points from the early 1970s.
Excessive fuel usage in everything from long-haul trucking to last-mile delivery, traffic congestion, and poorly planned routes contribute to higher CO2 emissions. At the same time, regulatory pressure and consumer demand for more sustainable business practices are forcing companies to adapt.
The Basics of Route Optimization
Route optimization tools use advanced algorithms and predictive analytics, parsing historical and real-time data to identify the most efficient delivery routes. Factors taken into account include traffic conditions, weather, vehicle capacity, delivery windows, and road restrictions.
Many routing tools within a transportation management system (TMS) also include load optimization capabilities, enabling companies to maximize their available freight capacity and improve key metrics like revenue per mile, cost per delivery, and fleet utilization.
State-of-the-art route optimization tools employ dynamic multi-day route planning and scheduling across trucking modes, everything from LTL, TL, middle mile, last mile, private fleet and dedicated transportation services.
Reducing Fuel Consumption and Carbon Emissions
As route optimization enables companies to reduce the number of miles driven, an immediate, tangible benefit is a significant saving on fuel consumption.
These tools also allow drivers to avoid areas of traffic congestion, helping to improve on-time delivery performance. This not only reduces truck dwell time and, thus, tailpipe emissions, but also increases customer satisfaction.
By optimizing load capacity, companies can put fewer trucks on the road, further reducing fuel usage and emissions — further driving sustainable logistics.
The Role of Real-Time Data in Sustainable Routing
Access to real-time data on traffic, weather, and road conditions allows for dynamic rerouting to avoid delays and minimize emissions. Traffic data can come from GPS systems and platforms like Google Maps or Waze for information on congestion, accidents, and road closures.
Weather data from apps like The Weather Channel or OpenWeatherMap provide updates on conditions (thunderstorms, high wind, fog, snow) that might affect a trip, rerouting if necessary. Telematics and sensors take in data on vehicle location, speed, fuel usage, and status from onboard systems or fleet management software.
Updates from order management systems (OMS) on delivery windows and customer availability also become part of the routing equation, as does data on weight or height restrictions and road closures from transportation departments. Routing software also tracks fuel efficiency and vehicle performance, reducing environmental impact.
Other Benefits of Route Optimization
In addition to reduced fuel consumption and lower operating costs, route optimization enables faster, more reliable deliveries, improving customer relationships and fostering loyalty.
Optimized routing also helps companies meet their environmental goals through sustainable logistics. This includes compliance with government regulations and qualification for certifications such as LEED, ISO14001, and SmartWay.
Route Smarter, Stay Greener
Route optimization improves logistics efficiency and plays a crucial role in reducing carbon emissions. An investment in this technology helps drive both sustainability and competitiveness in a business climate that increasingly values environmental responsibility. By embracing sustainable logistics practices through the use of these tools, companies can reach their goals while driving down costs through efficiency gains.
Tramm, an innovator in supply chain technology, has developed an end-to-end TMS platform that combines route planning, load building, transporter management, a supply chain control tower, and a powerful mobile app. With this end-to-end approach, Tramm has solved the problem of fragmented supply chain systems by integrating key functions into a unified, scalable platform.
Tramm’s Planning and Optimization Module handles complex routing environments, accounting for variables such as rules and constraints that accurately reflect on-the-ground transport operations. It allows users to easily adapt their plans based on changing needs, including “what if” visualization and scenarios that enable real-time adjustments. A load builder/stackability app lets them automatically plan loads that are tightly synced with capacity and route optimization.
To find out how Tramm’s unified approach can drive transportation efficiency and cost savings while helping you realize sustainability goals, request a demo today.
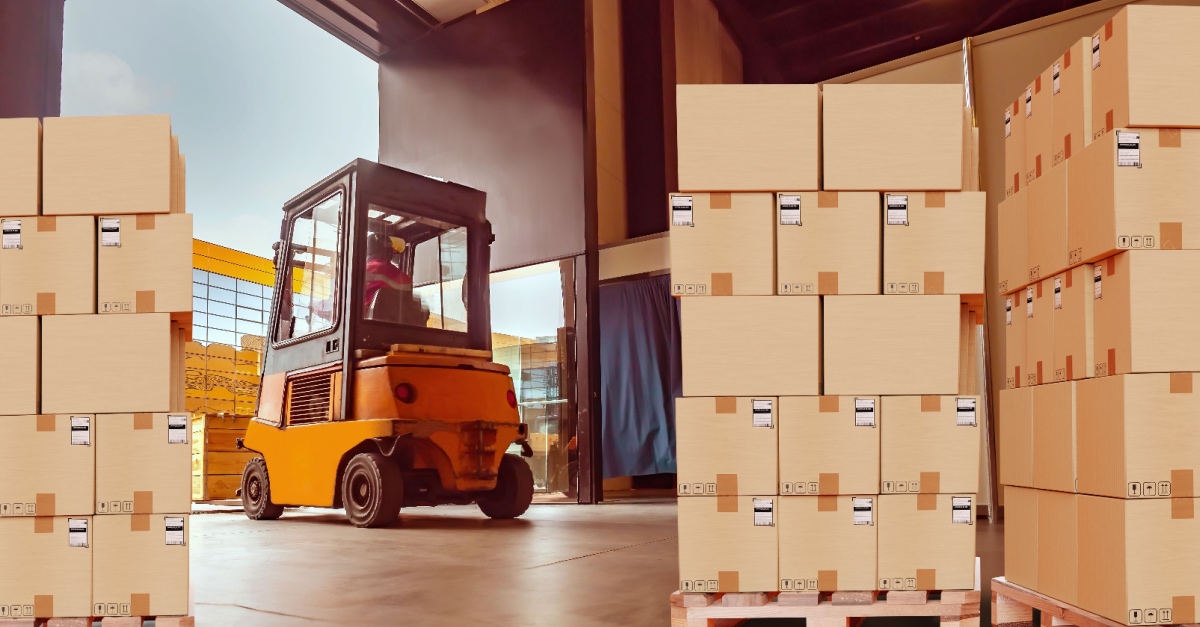
Managing Large Order Loads to Reduce Split Shipments
In the world of B2B commerce, having an efficient order management process is a baseline capability. Especially when large order loads are involved, the ability to achieve a high percentage of orders shipped complete drives significant transportation savings, as split shipments eat away at margins.
There are several factors that drive an increased reliance on split shipments for large order loads, sometimes acting in combination to exacerbate the issue. These include how inventory is distributed in a network, the pressure on stock levels from large orders, and the operational strain it can cause. That’s why order management precision and efficiency is at such a high premium, especially when disruptions like a major port strike throw a wrench in the works.
This article examines split shipments and the issues they cause within the supply chain and distribution and explores some best practices to avoid them. The aim is to help reduce operating expenses, improve product availability, and increase customer satisfaction.
Definition and Causes of Split Shipments
A split shipment happens when an order is divided into multiple shipments due to low stock levels, logistical constraints, or both. Often, businesses feel forced to ship what’s available immediately and send the rest later, hoping that customers can get by on the partial order in the meantime.
Some common causes of split shipments on large B2B orders include the following:
- Multiple suppliers: Variations in supplier lead times or stock availability can cause parts of the order to arrive at different times.
- Order complexity: Large orders often involve diverse products with different handling, storage, or shipping requirements. For instance, temperature-sensitive or hazardous goods requiring specialized transportation often lead to separate shipments.
- Order prioritization: High-priority, in-demand products are time-sensitive, which can lead to shipping what’s on hand separately while waiting for replenishment to send the rest.
- Warehouse fulfillment: Large orders can tax the resources of warehouse operations. SKUs stored in different locations or those requiring a different picking process can cause delays, leading to split shipments.
- Backorders and lead time variation: Some items have significantly different supplier lead times, forcing businesses to ship only a portion of their available inventory and put the balance on backorder.
- Inefficient systems: Without an advanced order management system (OMS), businesses lack real-time inventory visibility across multiple locations. This leads to fragmented fulfillment decisions and more split shipments.
The High Cost of Split Shipments
While some split shipments are inevitable or unavoidable due to external factors, costs go up along with higher frequency. Transportation is clearly the highest direct cost, as it’s generally the second highest expense as a percentage after labor, and more trips are required. There’s also the added complexity of scheduling additional pickups with transporters.
Speaking of labor, split shipments also hit this cost center, as they lead to more man-hours spent preparing orders through picking and packing.
Indirect costs include damage to customer relationships and reputation and the potential loss of future business. B2B customers rely on complete orders to meet production schedules or product demand. As a result, many retailers have implemented on-time in-full (OTIF) requirements. The idea is to enforce greater supply chain optimization by tight collaboration among retailers, brands, transporters, and logistics service providers.
Failure to meet OTIF requirements results in fines and penalties. A McKinsey study found that many retailers in North America are tightening OTIF requirements by narrowing delivery windows and increasing fines while revising the definition of in-full delivery.
A higher incidence of split shipments can reflect deeper issues of poor inventory management, such as stock imbalances or inefficient replenishment processes. Finally, they contribute to higher carbon emissions from the additional truck trips required.
Other Split Shipment Headaches in B2B
Split shipments introduce complexities that impact multiple areas of operations, including order tracking, invoicing, and customer communication. Each contributes to inefficiencies, often leading to higher costs, increased labor, and a decline in service quality.
Tracking Complexity
When shipments are split, tracking the order status becomes more complicated because different segments move independently through the supply chain. Logistics teams have to track each portion of the order separately, from inbound inventory to fulfillment and delivery. This involves monitoring multiple tracking numbers, the status of transporters, and estimated delivery times.
Managing Multiple Invoices
Split shipments often lead to multiple invoices, complicating accounts payable for both the shipper and customer, including reconciliation of multiple invoices against the original order. Each invoice might include different shipping costs, taxes, and fees, adding to administrative overhead. In some cases, customers might withhold payment until the entire order is delivered, adding more complexity and delaying closing the transaction.
Customer Communications
In B2B transactions, logistics and delivery impact a customer’s production schedules, inventory levels, and downstream operations. Shippers need to manage expectations around timing, coordination, and delivery schedules. Customers often rely on complete shipments to avoid production downtime, which causes frustration and the pain of adjusting internal processes.
Split shipments also require customers to coordinate with receiving teams across multiple deliveries. Additional labor and resources are needed to accept, inspect, and verify each portion of the order upon arrival.
Leveraging Technology to Optimize B2B Order Management
Advances in technology for supply chain and logistics have made it easier for businesses to optimize their inventory and order management processes in order to reduce the incidence of split shipments. Here are some examples.
WMS
A warehouse management system (WMS) provides real-time updates on inventory levels, enabling better decision-making and reducing stock-outs that lead to split shipments. Most systems can also automate inventory replenishment to ensure that items in high demand remain in stock, reducing the need for split shipments.
OMS
An order management system (OMS) integrates order data from various sources (e-commerce platform, ERP, CRM, WMS, etc.), providing visibility into inventory availability. This helps drive a higher percentage of “order complete” confirmations before shipment. An OMS also has consolidation logic for prioritizing full order fulfillment vs. partial shipments.
Tramm, a developer of a leading unified supply chain management platform, combines a powerful OMS within its transportation management system (TMS) suite. This integrated approach provides end-to-end visibility and control over order fulfillment and shipping processes. Tramm’s Order Management Module ensures that orders are fully consolidated before being released for shipment, while the TMS manages transportation in the most efficient, cost-effective manner.
Using real-time data synchronization, Tramm’s integrated approach ensures that any changes in order status, inventory levels, or shipping schedules are immediately reflected across both systems. This allows the OMS to quickly adjust fulfillment strategies if stock availability or transporter issues arise, reducing the need to rely on split shipments.
Predictive Analytics and Demand Forecasting
Predictive analytics tools tap the power of AI to enable proactive inventory management. By more accurately forecasting demand and optimizing inventory levels, both stockouts and split shipments are reduced. This technology enables users to foresee potential supply chain disruptions and adjust fulfillment strategies accordingly.
Automated Fulfillment and Transporter Routing
Fulfillment automation reduces errors in picking/packing, allowing a higher percentage of full orders to be processed and minimizing the need for split shipments.
Smart routing automatically directs orders to the most appropriate warehouse or fulfillment center, optimizing shipments and reducing transportation costs. Tramm’s Planning & Optimization Module uses advanced algorithms and visualization tools to drive better, faster load and routing decisions. The result is operational cost savings, including reduced split shipments and highly responsive planning capabilities.
Supplier Collaboration and Data Sharing
Collaborative planning includes sharing inventory and demand data with suppliers, improving stock replenishment, and reducing the likelihood of split shipments. By employing Vendor-Managed Inventory (VMI), suppliers manage stock levels, helping ensure that products are consistently available. This minimizes the need for split shipments due to out-of-stocks.
Best Practices to Minimize Split Shipments in B2B Order Management
Companies can take several steps to improve their order management processes, increase efficiency, and increase the percentage of “shipped complete” orders.
Centralized Inventory Management
Centralized inventory involves keeping all stock in one primary location, such as a warehouse, fulfillment center, or other storage facility. This central hub typically manages not only inventory but also key logistics functions like order processing and fulfillment.
In a centralized inventory system, the majority of operations, including order management and distribution, are handled from this single location, even when there are multiple sales channels or retail outlets. This strategy reduces the need for split shipments due to inventory imbalances.
Order Consolidation Policies
Order consolidation involves combining multiple orders into a single shipment. This can be done by centralizing items from multiple orders into a single location or by combining multiple orders from different sales channels into a single system.
Order consolidation can benefit businesses in several ways. This includes lower transportation costs based on economies of scale, better management of stock levels due to fewer shipments, overall simplified logistics, and a better customer experience through more complete orders.
Smart Reordering Strategies
Smart reordering is a rules-based, automated process utilizing data analytics and AI to manage inventory levels and optimize replenishment. Unlike traditional reordering, which relies on manual tracking or fixed schedules, smart reordering uses real-time data (sales trends, demand forecasting, lead times, supplier performance, etc.) to predict when SKUs will need to be replenished.
This approach helps ensure that critical and/or high-demand products are always in stock, preventing backorders and reducing the need for split shipments.
Transparent Customer Communication
This seems like an obvious point, but too many organizations fail to keep customers updated on order status. This is especially important when unexpected drops in inventory levels or logistics snafus require a split shipment.
Always give customers the option of waiting for replenishment to send a complete order or receiving a partial shipment first. In some cases, the added expense of expedited transportation comes into play to make things right and keep to their schedule.
Continuous Monitoring and Adjustment
Regularly analyzing order data helps identify patterns that lead to increases in split shipments. By tracking trends in demand, stock levels, and fulfillment performance, you can proactively adjust inventory management, including redistributing stock across locations or improving order consolidation processes.
Leaning On Technology to Optimize Large Order Loads
Minimizing split shipments is important to maintain supply chain efficiency and reduce transportation costs. Software such as OMS, WMS, and predictive analytics tools can improve inventory management and streamline fulfillment processes. Best practices such as smart reordering, order consolidation, and continuous monitoring help reduce the incidence of split shipments.
Tramm integrates transporter management, route optimization, order management, customizable dashboards, and a control tower to optimize routing and order allocation. When shipments do need to be split, Tramm automates the process based on operational and resource requirements.
Tramm’s FleetVision Module gives users access to precise real-time data and insights. With a better understanding of fleet operations on a granular level, they can manage each load more effectively and implement performance improvement measures. The result is greater efficiency, reduced costs, and improved customer satisfaction.
To learn more about how Tramm can drive measurable improvement in your supply chain and logistics operations, request a demo today.
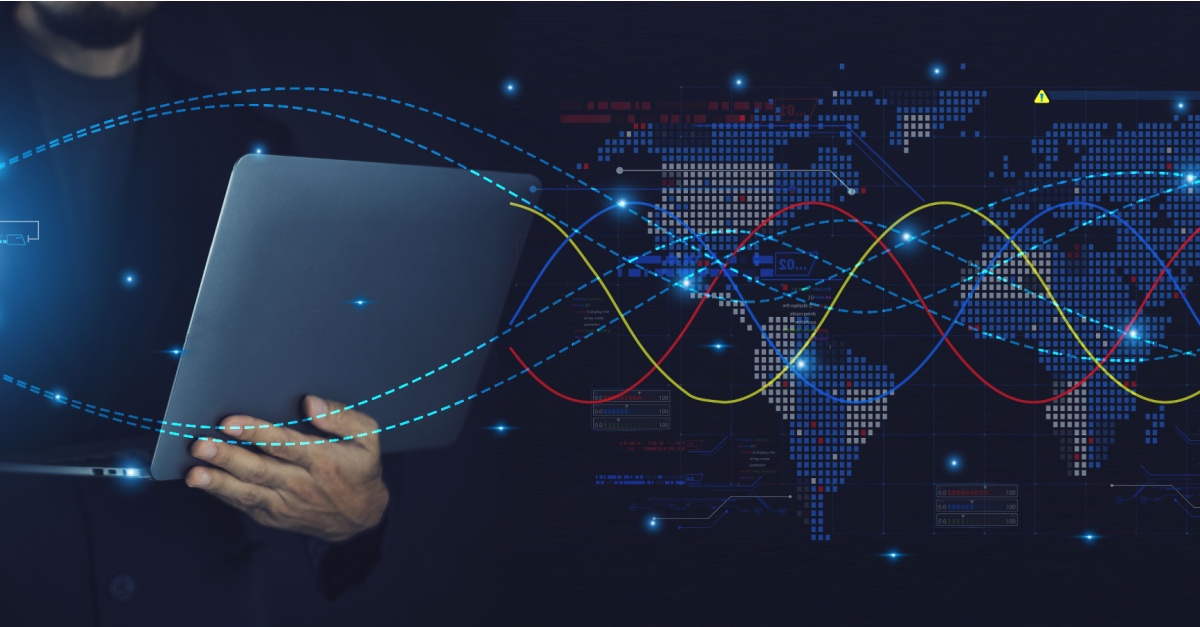
Improving Strategic Decision-Making in Logistics With Advanced Analytics
Years back, UPS had a catchy marketing tagline that said, “We Love Logistics.” Well, given the complexity and increasing demands on logistics and supply chain teams, you had better love it, as it’s a highly demanding discipline. This is why decision-making in logistics needs advanced analytics backup: There’s little margin for error when contracts and valuable customer relationships are riding along with each delivery.
Advanced analytics are, in fact, transforming logistics processes in everything from route optimization to driver hours of service, dispatch and delivery, transporter selection, and even yard management. Among the many benefits of this kind of digital approach are greater operational efficiency, lower costs, and improved customer satisfaction.
The Role of Advanced Analytics in Strategic Logistics Decisions
Advanced analytics uses sophisticated techniques and tools to analyze data, uncover deep insights, predict trends, and improve decision-making. It goes beyond simple descriptive analytics or a summary of historical data, using methods that provide actionable outputs and strategic guidance.
Predictive analytics, as the name implies, involves using statistical models and machine learning algorithms to forecast future outcomes based on patterns in historical data. The next step beyond that is prescriptive analytics, which recommends specific actions to achieve desired outcomes through analysis of potential scenarios and their implications.
Helping power decision-making in logistics, control towers have risen in importance as a way to manage the complex flow of inbound/outbound assets, loads, and team members. Primarily, it’s a centralized hub that provides end-to-end visibility, real-time monitoring, and coordination of supply chain activities. Logistics managers access a control tower to track shipments, manage exceptions, and make data-driven decisions geared toward optimized operations.
How Analytics Lead To Better Logistics Decision-Making
Advanced analytics plays a transformative role in optimizing transportation and delivery. Here are specific examples that highlight its impact:
Route Optimization
Real-time analytics assess traffic patterns, weather conditions, and fuel costs, as well as factors like delivery windows and vehicle/site/production restrictions, to determine the most efficient routes. For example, a transporter uses GPS-enabled analytics to avoid congested roads, helping speed up delivery and reduce fuel costs.
Route optimization tools leverage advanced algorithms to improve load planning and cross-docking. They can also optimize planning for multi-modal transportation (LTL and FTL, box trucks and sprinter vans for last mile, etc.), multi-day, and multi-fleet scenarios.
ETA Predictions and Updates
Analytics integrates real-time tracking and other telematics data and compares it with planned data and historical patterns to provide accurate delivery ETAs. Transporters and couriers use advanced analytical models to provide updates on delays due to traffic or bad weather, improving transparency and satisfaction.
Evaluating Transporter, Fleet Performance
Advanced analytics help assess and improve both transporter and fleet performance. By tracking key metrics such as on-time delivery rates, claims for damaged goods, and cost efficiency, shippers gain valuable insights into transporter reliability and efficiency. These metrics help identify high-performing carriers and drivers, enabling shippers to negotiate favorable contracts and foster long-term partnerships.
For fleet drivers, analytics can evaluate metrics on adherence to schedules, fuel efficiency, safety records, and driving behaviors like braking or speeding. This helps maintain high standards while identifying areas for training or improvement.
Integrated analytics can also consolidate data across all third-party and fleet operations. This helps shippers optimize fleet utilization, balance workloads, and replace underperforming drivers or carriers, enhancing supply chain's performance and reliability.
Shipment Consolidation and Load Optimization
Data models analyze shipment volumes and destinations to maximize cube utilization and reduce the number of trips. Logistics providers can use this advanced modeling to consolidate LCL freight from multiple shippers heading to the place, lowering operating costs and simplifying scheduling.
Best Practices for Implementing Analytics in Logistics
Successfully integrating analytics into logistics operations requires strategic alignment and thoughtful execution. Start by fostering a data-driven culture. All teams, from operations to management, must understand the value of analytical decision-making. This kind of mindset shift is essential for embracing data analytics as a core part of the logistics workflow.
Invest in integrated technology to streamline data flow and visibility. Combining analytical tools with assets like a Transportation Management System (TMS), a Warehouse Management System (WMS), and a logistics control tower contributes to greater efficiency by consolidating multi-source data. Integrating these complementary systems in a logistics tech stack facilitates seamless communication and better analytical outcomes.
Prioritize quality, real-time data to enable responsive decision-making. Determine what kind of data you need and how often you need it. Do you need weekly or daily logistics reports, or do you need up-to-date information every time you log into the dashboard? Access to real-time data analytics lets you monitor and analyze trends over time, allowing you to better respond to opportunities and eliminate inefficiencies.
Better Decision-Making in Logistics, Fueled By Advanced Analytics
Analytics are transforming logistics by enabling data-driven decisions that improve efficiency and customer satisfaction. Predictive and prescriptive analytics help forecast trends and recommend strategies to address challenges such as route optimization, transporter selection, and improving on-time performance.
A logistics control tower offers comprehensive, real-time visibility into logistics and supply chain activities. Integrating it with TMS and WMS, overlaid with analytics, helps logistics teams reduce costs and respond faster to disruptions and market shifts.
Tramm, an innovator in supply chain technology, has developed an end-to-end TMS platform that combines order management, route planning and load building, transporter management, a logistics control tower, and a powerful mobile app. With this comprehensive approach, Tramm has solved the problem of fragmented supply chain systems by integrating key functions into a unified, scalable platform. Tramm’s business intelligence tools increase performance at the fleet and driver level by empowering data-driven decision-making.
To find out how Tramm’s unified platform and advanced analytics can help you drive transportation efficiency and improve decision-making in logistics, request a demo today.
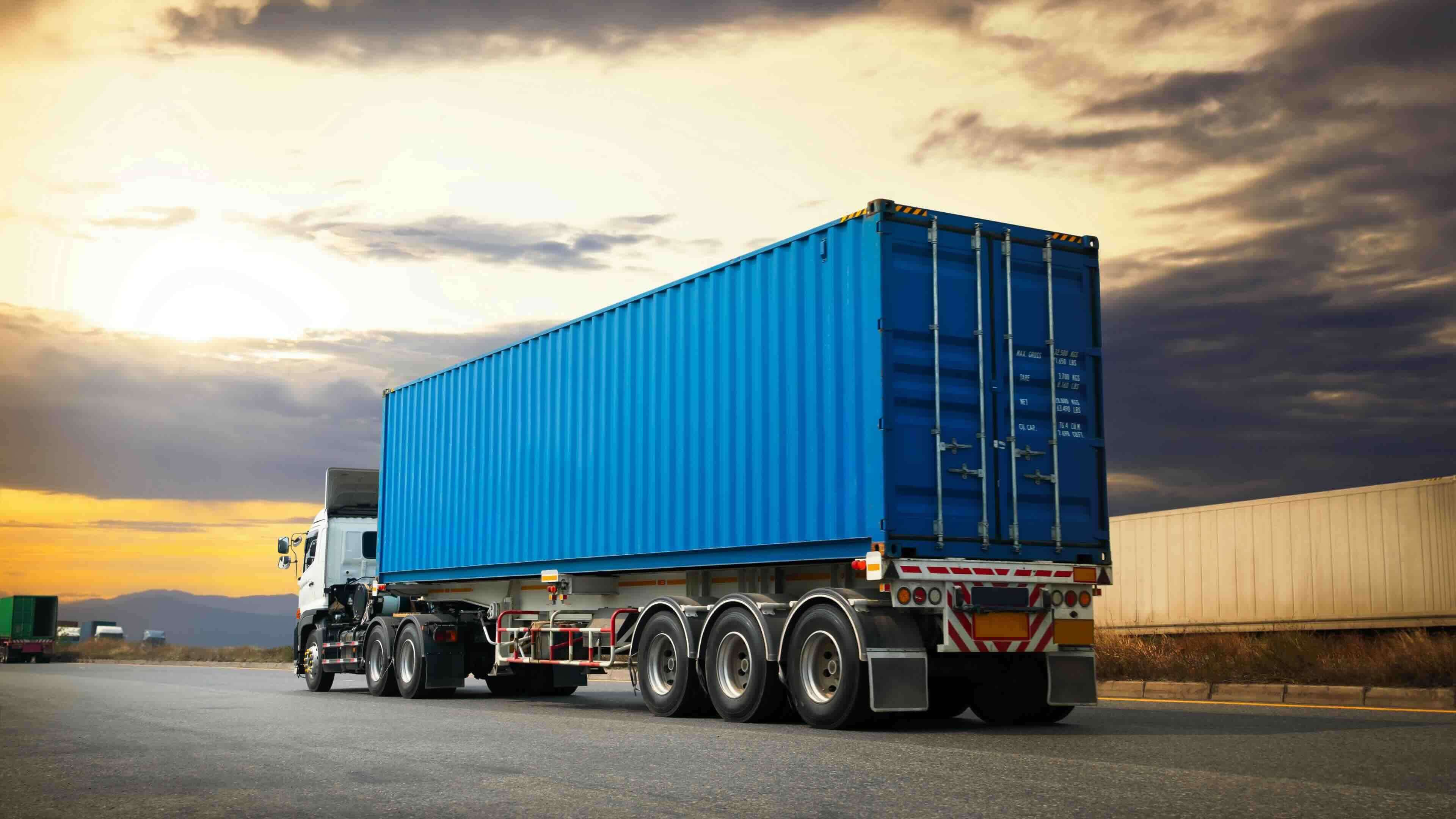